How to Optimize 3 Axis CNC Scheduling for Better Workflow
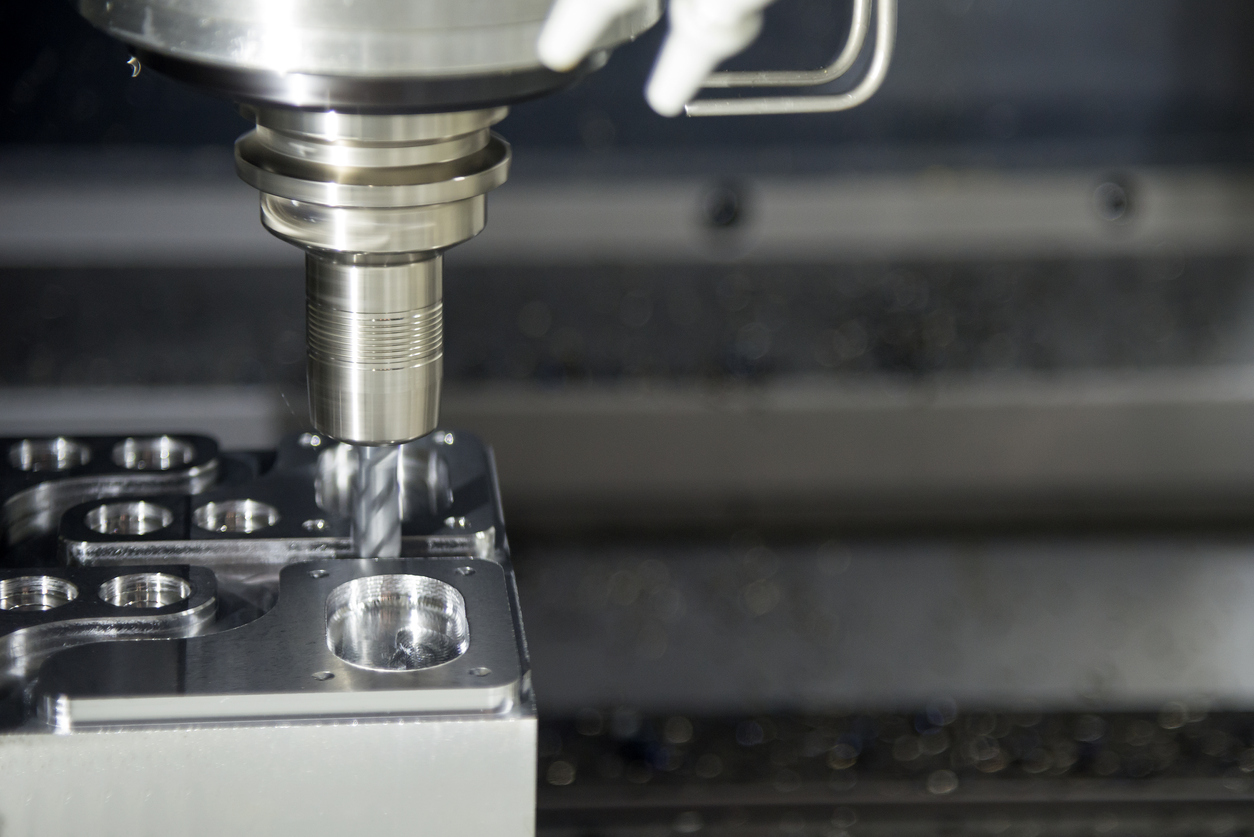
In today's fast-paced manufacturing landscape, efficiency is paramount. For machine shops and prototyping facilities, optimizing 3-axis CNC scheduling can be the key to unlocking higher productivity and delivering exceptional results to clients.
By mastering the art of 3-axis CNC scheduling, manufacturers can streamline their operations, reduce downtime, and maximize machine utilization. This strategic approach to planning and organizing machining tasks is essential for staying competitive in an ever-evolving industry.
In this article, we'll explore the intricacies of 3-axis CNC scheduling, delving into best practices, cutting-edge techniques, and the latest software solutions designed to revolutionize your manufacturing processes.
What is 3 Axis CNC Scheduling?
3-axis CNC scheduling is the strategic planning and organization of machining operations on three-axis CNC machines to optimize workflow, enhance efficiency, and maximize machine utilization. This process involves carefully orchestrating the sequence of machining tasks, taking into account critical factors such as toolpath planning, feedrate scheduling, and machine setup.
The primary goal of 3-axis CNC scheduling is to ensure that machines are running at peak efficiency, minimizing downtime and maximizing output. By strategically planning the order and timing of machining operations, manufacturers can reduce setup times, optimize tool changes, and minimize unnecessary machine movements.
Effective 3-axis CNC scheduling requires a deep understanding of the machining process, the capabilities of the CNC machines, and the specific requirements of each job. It also involves leveraging advanced techniques and software solutions to streamline the scheduling process and adapt to changing priorities and demands.
How to Optimize 3 Axis CNC Scheduling
Achieving optimal efficiency in 3-axis CNC operations requires a strategic approach to scheduling that prioritizes precision and adaptability. By refining scheduling practices, manufacturers can better align their production processes with operational goals, ultimately driving greater throughput and quality.
Core Elements of Streamlined Scheduling
Effective 3-axis CNC scheduling hinges on three essential components: optimizing the path of the tool, calibrating feedrate adjustments, and refining machine preparation. Each of these elements is integral to the seamless operation of CNC machinery.
- Toolpath Optimization: Developing precise toolpaths minimizes redundant machine movements, cutting down on production time and reducing tool wear. Leveraging simulation software for toolpath planning can significantly enhance the accuracy and efficiency of machining operations.
- Feedrate Calibration: This involves fine-tuning the speed of the cutting tool across the material, employing methods such as sliding arc tube (SAT) to pinpoint areas where feedrate adjustments are necessary. This ensures machining processes maintain a balance between speed and precision, ultimately enhancing overall productivity.
- Machine Preparation: Ensuring that machines are set up accurately and swiftly is crucial for reducing idle time. Standardized setup protocols facilitate consistency across operations, while staying abreast of industry advancements ensures that setup practices remain cutting-edge.
By focusing on these core elements, machine shops can refine their scheduling strategies to maximize the capabilities of their 3-axis CNC machines. This approach not only enhances operational efficiency but also ensures that production processes are resilient and responsive to evolving industry demands.
Step 1: Analyze the Workflow
To enhance the efficiency of 3-axis CNC operations, begin by conducting a thorough mapping of the entire machining process. This involves detailing each phase from the initial setup through to the final production, allowing for a comprehensive understanding of the workflow. The goal is to uncover specific areas where delays or inefficiencies might occur, enabling targeted improvements.
Assessing the Current System
Undertake a detailed examination of the current scheduling mechanisms to identify potential areas of refinement. Focus on how resources such as machine time, labor, and materials are utilized, and assess whether there is a seamless alignment between planned schedules and actual operations. This review should reveal discrepancies that can be addressed to enhance overall efficiency.
Strengthening Coordination Practices
Improving coordination across departments can significantly enhance CNC operations. Establish robust communication channels among teams involved in the machining process—such as design, production, and quality assurance. Regular updates and collaborative sessions can align efforts and minimize errors or misalignments. By fostering a culture of open communication, you can ensure that all stakeholders are informed and operations proceed without unnecessary interruptions.
By conducting a thorough workflow analysis and addressing inefficiencies, manufacturers can lay the groundwork for more advanced scheduling solutions. This initial step is crucial for setting the stage for more effective CNC process management and improved production outcomes.
Step 2: Implement Feedrate Scheduling Techniques
Refining feedrate scheduling is essential for achieving enhanced accuracy and operational efficiency in 3-axis CNC machining. By adopting innovative scheduling strategies, manufacturers can fine-tune the relationship between machining speed and precision, aligning tool operation with material characteristics. This requires a targeted approach to adjusting feedrate parameters, tailored to the specific demands of each machining task.
Innovative Approaches for Enhanced Performance
Utilizing advanced methodologies such as parametric curve-based planning can significantly improve feedrate scheduling. This involves delineating sections of the toolpath where feedrate modulation is critical, ensuring optimal cutting conditions are maintained. By leveraging these methodologies, manufacturers can customize feedrate alterations to match the intricacies of varying machining requirements.
- Parametric Curve Planning: This technique allows for the creation of smooth transitions in feedrate adjustments. By utilizing curves to govern the toolpath, this method reduces abrupt changes in feedrate, thereby enhancing the fluidity and efficiency of the machining process.
- Adaptive Scheduling Systems: Implement systems that dynamically adjust feedrate based on real-time machining data. These systems enable the CNC machine to automatically adapt to fluctuations in material properties or tool conditions, thereby maintaining peak cutting performance.
Harnessing Technological Advancements
Regularly engaging with emerging digital manufacturing trends is vital for optimizing feedrate scheduling practices. By staying updated on industry breakthroughs and technological innovations, manufacturers can integrate state-of-the-art techniques into their operations. This continuous learning approach empowers manufacturers to maintain a competitive edge in precision and efficiency.
Integrating these advanced feedrate scheduling techniques into CNC processes not only streamlines operations but also elevates the quality of the output. By focusing on adaptability and innovative methodologies, manufacturers can achieve superior operational outcomes, ensuring their CNC machining processes remain efficient and effective.
Step 3: Optimize CNC Toolpath Planning
Enhancing the precision and efficiency of CNC operations significantly depends on the innovation within toolpath planning. By crafting toolpaths that are optimized for the task, manufacturers can enhance productivity and reduce wear on machinery. This optimization involves a keen understanding of machining dynamics and the specific requirements of each project.
Advanced Path Configuration
To maximize efficiency, it's essential to implement advanced path configuration strategies. This includes designing paths that enable efficient material removal, thus reducing time and machine strain. Utilizing modern CAD/CAM software provides a platform for visualizing potential paths and making necessary refinements before production begins.
- Efficient Material Engagement: Ensure paths are configured to engage material effectively, minimizing unnecessary tool engagement and maximizing cutting efficiency.
- Seamless Movements: Develop paths that facilitate fluid machine movements, reducing mechanical load and improving the final product's integrity.
Utilizing Predictive Tools
Predictive tools are crucial in refining toolpath strategies. These tools simulate the machining process, allowing for the identification of potential inefficiencies or conflicts in the path design. Through predictive modeling, adjustments can be made to ensure alignment with production objectives, ultimately enhancing the workflow.
The impact of innovative toolpath planning extends beyond immediate gains. It enhances the overall effectiveness of machining operations, ensuring that components meet stringent quality standards with minimal waste. By integrating advanced path configuration and predictive tools into planning processes, manufacturers can elevate their CNC operations to new heights of accuracy and efficiency.
Step 4: Enhance Machine Setup Procedures
Streamlining the transition between machining tasks involves more than just quick setups—it requires precision and adaptability. To achieve operational excellence, manufacturers should focus on refining setup strategies that align with specific production goals and machine capabilities.
Tailored Procedures for Efficiency
Adopting tailored setup procedures ensures that each machine is prepared optimally for its designated tasks. This involves crafting specific protocols that address the unique needs of each operation, from initial adjustments to final checks. By customizing these processes, manufacturers can enhance the efficiency and accuracy of machine setups.
- Create Task-Specific Protocols: Develop protocols that cater to the particular requirements of each machining task, ensuring that setups are aligned with operational objectives.
- Utilize Advanced Training Modules: Implement training modules that focus on the latest techniques and tools, equipping operators with the knowledge required to execute setups efficiently.
Integrating Emerging Technologies
Incorporating cutting-edge technologies into setup procedures provides a significant advantage in maintaining competitiveness. This requires a proactive approach to evaluating new tools and methods that can be integrated into existing processes, enhancing both precision and productivity.
- Explore Innovative Tools: Regularly assess new tools and technologies that can improve setup processes, ensuring that operations leverage the best available resources.
- Engage with Industry Experts: Collaborate with industry experts to gain insights into emerging trends and best practices, facilitating the integration of innovative solutions into setup procedures.
By adopting tailored procedures and integrating emerging technologies, manufacturers can optimize their CNC operations, ensuring that setups are not only efficient but also aligned with the latest industry advancements.
Step 5: Utilize CNC Scheduling Software
Implementing CNC scheduling software brings a transformative edge to managing complex machining operations, offering seamless coordination of tasks and enhancing productivity. This advanced software automates the intricate details of scheduling, allowing manufacturers to focus on strategic decision-making while ensuring production remains efficient and responsive to dynamic needs.
Real-Time Monitoring and Flexibility
Choosing CNC scheduling software with robust real-time monitoring and adaptability is crucial. Such features provide a comprehensive view of ongoing operations, enabling swift modifications to schedules in response to real-time data. By maintaining this level of oversight, manufacturers can optimize machine use and swiftly address any production variances.
- Adaptive Resource Management: Software that enables quick reallocation of tasks ensures operations adapt smoothly to changes, reducing potential downtime.
- Enhanced Utilization: Real-time monitoring of machine status aids in optimizing resource deployment, ensuring that both machines and personnel are engaged effectively.
Leveraging Data for Strategic Improvements
Incorporating analytics from scheduling software into operational strategies allows for ongoing refinement and enhancement of scheduling processes. Through detailed data analysis, manufacturers can uncover patterns and areas for enhancement, driving more strategic scheduling efforts.
- Comprehensive Reporting: Use in-depth reports generated by the software to assess machine performance and identify potential inefficiencies or bottlenecks in the workflow.
- Predictive Analytics: Employ predictive capabilities to anticipate future production needs, enabling proactive schedule adjustments aligned with projected demands.
Through the strategic deployment of CNC scheduling software, manufacturers can achieve a harmonized and efficient production environment. This integration not only bolsters operational flexibility but also supports a data-informed approach to continuous improvement, keeping CNC processes aligned with industry advancements.
By embracing these strategies for optimizing 3-axis CNC scheduling, you can unlock new levels of efficiency and productivity in your manufacturing operations. As technology continues to evolve, staying ahead of the curve is essential for maintaining a competitive edge in the industry. If you're ready to revolutionize your CNC scheduling processes, schedule a demo or try the platform to experience its capabilities and see how we can help you achieve your manufacturing goals.