Achieving Precision: Quality Control Strategies for 5 Axis Systems
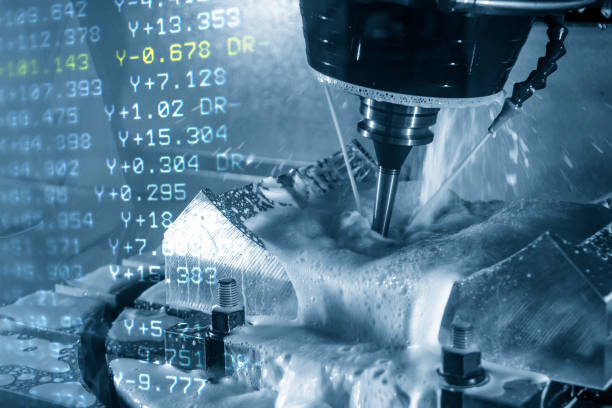
In today's manufacturing landscape, the demand for complex and precise components has never been higher. As industries like aerospace, medical, and automotive push the boundaries of design and functionality, the need for advanced machining techniques becomes paramount. Enter 5-axis CNC machining—a cutting-edge technology that enables the creation of intricate geometries with unparalleled accuracy and efficiency.
However, with great capability comes great responsibility. To truly harness the power of 5-axis machining, manufacturers must prioritize quality control at every stage of the process.
This article delves into the world of 5-axis quality control, exploring the strategies, techniques, and best practices that ensure the highest level of precision and consistency in every machined component. From machine calibration to inspection methods, we'll cover the essential elements that contribute to a successful 5-axis machining operation.
What is 5 Axis Quality Control?
5-axis quality control refers to the comprehensive process of ensuring precision and accuracy in machining processes using 5-axis CNC machines. This involves utilizing advanced techniques, tools, and standards to monitor and maintain the high-quality output of complex geometrical components, crucial for industries requiring meticulous detail and precision.
5-axis machining introduces additional complexity compared to traditional 3-axis machining. With the ability to move the tool or workpiece in five different axes simultaneously, 5-axis machines can create more intricate shapes and contours. However, this increased flexibility also demands a higher level of quality control to ensure that the final product meets the required specifications.
Effective 5-axis quality control encompasses a range of strategies, including:
- Machine Calibration: Regular calibration of the machine's geometry and compensation for any deviations to maintain accuracy throughout the machining process.
- Tool Management: Selection of appropriate cutting tools for specific materials and operations, as well as monitoring tool wear and implementing automatic compensation.
- Workpiece Positioning: Precise alignment and secure clamping of the workpiece to minimize vibrations and ensure consistent machining results.
- CNC Programming: Optimization of tool paths and machining parameters using advanced CAM software to achieve the desired geometry while minimizing machining time and tool wear.
- In-Process Measurement: Real-time monitoring of critical dimensions and surface quality during the machining process to identify and correct any deviations.
- Post-Machining Inspection: Thorough measurement and analysis of the finished component using advanced metrology tools like coordinate measuring machines (CMMs) to verify compliance with the required tolerances.
By implementing these quality control measures, manufacturers can ensure that their 5-axis machining processes consistently deliver high-precision components that meet the exacting standards of their customers. This not only enhances the quality of the final product but also reduces waste, minimizes rework, and improves overall operational efficiency.
Achieving unparalleled precision in 5-axis quality control demands a deep understanding of the complexities inherent in producing intricate geometries. The advanced capabilities of 5-axis CNC machines allow for the creation of detailed parts, necessitating a high level of accuracy and consistency at every stage of production. As each additional axis introduces potential for variability, maintaining exacting standards is paramount.
In environments where exactitude is crucial, such as in the production of high-performance components, the role of quality control is indispensable. Deviations, even on a minuscule scale, can result in significant operational challenges, particularly in fields like aerospace and biotechnology. A structured approach to quality control not only ensures compliance with dimensional specifications but also fortifies product integrity and reliability.
Key to this precision is the implementation of an integrated quality control system. This involves advanced machine diagnostics and the application of cutting-edge measurement technologies. Employing real-time monitoring and comprehensive post-process evaluations enables early detection and rectification of discrepancies. By leveraging these sophisticated methodologies, manufacturers can consistently achieve the high precision necessary for complex and demanding applications.
Step 1: Calibration and Machine Maintenance
Achieving precision in 5-axis machining begins with a thorough approach to machine calibration and maintenance. Regular calibration ensures each machine component functions in harmony, maintaining the integrity of the machine's geometric configuration. By routinely validating the alignment of moving parts, manufacturers can safeguard against deviations that manifest as inaccuracies in the final product. This practice is essential for preserving the machine's high-performance capabilities over its operational lifespan.
Incorporating regular maintenance checks is vital for identifying potential wear and tear that might compromise machining accuracy. Key components such as spindle bearings and linear guides are subject to degradation from continual use. By scheduling periodic inspections, operators can detect and address early signs of wear, preventing costly interruptions and sustaining the machine's precision. Promptly replacing or servicing parts as needed ensures the machine operates smoothly and efficiently.
In complex machining tasks, precision errors often arise from compounded inaccuracies. Calibration serves as a crucial line of defense against such errors, ensuring that each machine axis performs with exactitude. In a 5-axis environment, where simultaneous multi-axis operations are routine, even the slightest misalignment can lead to significant discrepancies in the finished product. By consistently applying rigorous calibration standards, manufacturers can minimize these risks, thereby enabling the flawless execution of intricate designs.
Step 2: Tool Selection and Management
Precision in 5-axis machining begins with the judicious selection of cutting tools tailored to the material and specific machining operations. For example, harder alloys like titanium demand the use of robust, wear-resistant tools such as carbide, while softer materials like aluminum require sharper tools to achieve a pristine finish. This precise matching of tools to materials ensures optimal cutting performance and surface quality.
Implementing advanced monitoring techniques is crucial to managing tool wear effectively. As tools experience wear, their cutting efficiency can decline, risking defects in the finished product. By utilizing real-time monitoring systems, any deviations in tool performance can be detected early, allowing for timely interventions. This proactive approach helps maintain high-quality outputs and extends tool longevity, minimizing the need for frequent replacements.
Strategically optimized tool paths are vital for enhancing operational efficiency in 5-axis machining. By leveraging sophisticated CAM software, manufacturers can meticulously plan tool paths that reduce unnecessary movements and maximize cutting efficiency. This not only accelerates production cycles but also conserves tool life by maintaining consistent cutting conditions throughout the machining process. This integrated approach to tool selection and management is essential for achieving excellence in complex machining tasks.
Step 3: Workpiece Clamping and Positioning
The stability of the workpiece is paramount in 5-axis machining, where any displacement can lead to significant errors. Advanced clamping solutions are essential; implementing systems such as magnetic or pneumatic clamps ensures the workpiece remains steadfast during machining. These methods offer the necessary grip without causing damage, thus maintaining the integrity of the workpiece.
Accurate setup is crucial; small missteps in alignment can cascade into larger problems, particularly in the dynamic environment of multi-axis machining. Employing laser alignment systems or optical sensors can ensure the workpiece is positioned correctly before the machining begins. These technologies enhance setup accuracy, minimizing the risk of misalignment in subsequent machining stages.
Custom fixtures are vital for handling intricate geometries. These tailored solutions are crafted to accommodate the unique contours of complex parts, offering support where conventional fixtures might fail. By using custom fixtures, manufacturers can access challenging areas of the workpiece, ensuring comprehensive machining while preserving precision across the most detailed designs.
Step 4: CNC Programming
Maximizing the capabilities of 5-axis machining hinges on the adept use of CNC programming, where advanced software orchestrates the entire process with precision. This technology facilitates the creation of complex geometries by allowing seamless transitions between axes, ensuring each movement is deliberate and contributes to the desired output. By employing intelligent algorithms, manufacturers can simulate tool paths, providing a digital rehearsal that refines operations before actual machining commences.
Precision in CNC programming requires meticulous attention to machining parameters. Every material poses unique challenges, necessitating specific calibrations in speed and feed rate to achieve optimal machining conditions. This careful customization not only enhances cutting performance but also prolongs the life of the tools, ensuring that every operation maintains the highest standards of quality and efficiency.
Simulations prior to machining are indispensable for error prevention. These digital trials offer comprehensive insights into the machining sequence, allowing for adjustments that avert potential issues before they materialize. By proactively addressing these concerns, manufacturers can maintain an uninterrupted workflow, fostering a production environment where precision and reliability are consistently achieved.
Step 5: Measurement and Inspection
In the realm of 5-axis machining, the importance of precise measurement and inspection cannot be overstated. Employing cutting-edge measurement technologies during the machining process facilitates immediate detection of anomalies, allowing for swift corrective action. Advanced real-time data acquisition systems are integral in maintaining the desired machining conditions, thereby ensuring the fidelity of the production cycle.
After machining, comprehensive assessments are crucial to validate the integrity of the finished component. This involves conducting detailed analyses to confirm that all specifications have been met. Utilizing precision instruments such as laser scanners and profilometers provides a thorough examination of surface contours and dimensional accuracy. These tools help identify any inconsistencies, allowing for necessary adjustments before further processing or dispatch.
For complex geometries, the deployment of laser scanning technology offers significant benefits. This non-contact method captures detailed surface data, enabling a meticulous comparison with the original design files. The precision and efficiency of laser scanning make it an invaluable asset in the quality control toolkit, ensuring that every aspect of the component conforms to stringent industry standards.
Step 6: Environmental and Operator Considerations
Ensuring a stable environment is integral to achieving high precision in 5-axis machining. Variations in temperature can lead to thermal distortion, affecting both the machine and the workpiece. By implementing climate control systems, manufacturers can maintain consistent ambient conditions, thereby safeguarding the dimensional integrity of components. This approach not only enhances machining accuracy but also contributes to the longevity of equipment by mitigating thermal stress.
The role of operators is equally crucial in the 5-axis machining process. Comprehensive training equips them with the knowledge to anticipate and address machine and material behavior during operations. Skilled operators can adeptly manage tool changes and adjust machining parameters, optimizing the quality of the final product. Ongoing training programs are vital, ensuring operators remain well-versed in the latest techniques and technologies, fostering an atmosphere of continuous improvement.
The synergy between a controlled environment and an adept operator team forms the backbone of successful 5-axis machining. Together, they create a robust framework that supports precise operations, reduces the likelihood of errors, and sustains the reliability of manufacturing processes over time.
As you embark on your journey to achieve precision in 5-axis machining, remember that quality control is an ongoing process that requires dedication and attention to detail. By implementing the strategies and techniques discussed in this article, you can elevate your machining operations to new heights of accuracy and efficiency. If you're ready to take your manufacturing processes to the next level, schedule a demo or try the platform to experience how we can help you streamline your workflows and achieve unparalleled precision.