Navigating Additive Manufacturing Process Planning and Control
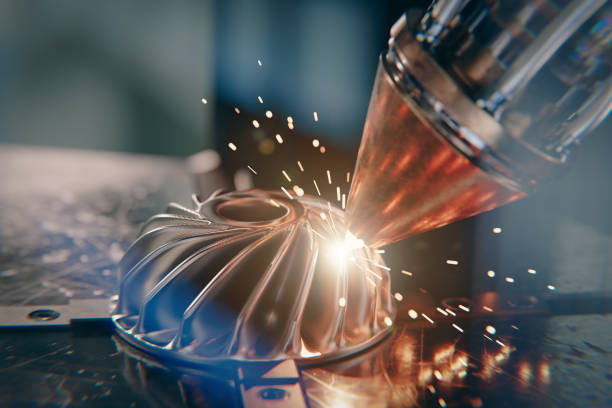
Additive manufacturing, also known as 3D printing, has revolutionized the way products are designed and produced. As this technology continues to evolve and mature, manufacturers are increasingly looking to adopt additive manufacturing processes for large-scale production.
However, integrating additive manufacturing into existing production lines and scaling up operations presents unique challenges. Effective production planning becomes crucial to ensure efficiency, quality, and cost-effectiveness.
In this article, we will explore the key considerations and best practices for additive production planning. We will delve into the strategies and techniques that can help manufacturers optimize their additive manufacturing processes and achieve their production goals.
What is Additive Manufacturing Process Planning and Control?
Additive manufacturing process planning and control is a systematic approach to managing and optimizing the workflow in 3D printing operations. It encompasses a wide range of activities, from planning post-processing tasks to conducting quality assurance checks and managing logistics. The primary objective is to ensure smooth and efficient operations while addressing the unique challenges posed by additive manufacturing technology.
Effective process planning and control in additive manufacturing requires careful consideration of various factors, such as machine utilization, material management, and resource allocation. Unlike traditional manufacturing methods, additive manufacturing allows for greater design freedom, customization, and complex geometries. However, it also introduces new variables and constraints that need to be accounted for during the planning phase.
Key components of additive manufacturing process planning and control include:
- Post-Processing Planning: Additive manufacturing often requires post-processing steps to achieve the desired part quality and functionality. Planning these tasks efficiently is crucial to minimize lead times and ensure timely delivery.
- Quality Assurance: Maintaining consistent part quality is essential in additive manufacturing. Quality assurance checks need to be integrated into the production planning process to identify and address any issues early on. This may involve implementing in-process monitoring, conducting dimensional inspections, or performing material testing.
- Logistics Management: Additive production planning also involves managing the flow of materials, parts, and information throughout the manufacturing process. This includes inventory management, scheduling, and coordination with other departments or suppliers. Efficient logistics management helps to minimize delays, reduce waste, and ensure smooth operations.
By implementing effective additive manufacturing process planning and control, manufacturers can reap several benefits, such as increased efficiency, cost reduction, enhanced quality, and improved customer satisfaction. To achieve these benefits, manufacturers need to adopt a systematic approach that leverages advanced planning tools, data analytics, and automation technologies to streamline processes and make informed decisions - like we offer at Phasio.
How to Navigate Additive Manufacturing Process Planning and Control
Navigating additive manufacturing process planning and control involves establishing a methodical framework that addresses the intricate nature of this advanced production technique. Leveraging the adaptability and complexity of additive manufacturing necessitates an organized strategy that ensures smooth operations and consistent results. This approach integrates cutting-edge methodologies and tools that facilitate seamless transitions from design to the final production stage.
Establish a Comprehensive Workflow
Creating an effective roadmap for additive manufacturing processes ensures operational consistency and enhances efficiency. This roadmap should encompass all production phases, from the conceptual design to the final product inspection. Employing specialized workflow management systems tailored for additive manufacturing significantly boosts operational efficiency. These systems provide functionalities such as comprehensive data integration, automated task scheduling, and resource coordination, ensuring that each production stage aligns with the overall strategic objectives.
Components of a Robust Workflow:
- Design for Functionality: Focus on optimizing designs specifically for additive capabilities, emphasizing features like weight reduction and material efficiency.
- Integrated Data Systems: Use platforms that unify data from different production stages, enhancing decision-making capabilities.
- Continuous Improvement Mechanisms: Implement feedback systems that allow for ongoing adjustments and optimization of the manufacturing process.
Optimize Resource Allocation
Strategic resource allocation underpins the potential of additive manufacturing to deliver effective and timely production solutions. Identifying and deploying resources efficiently ensures cost-effectiveness and adherence to timelines. This involves a strategic distribution of materials, machine time, and human expertise to maintain a competitive advantage within the manufacturing sector.
Resource Optimization Techniques:
- Adaptive Resource Scheduling: Employ systems that adjust schedules dynamically in response to demand fluctuations and production priorities.
- Maximizing Equipment Efficiency: Enhance machine uptime through predictive maintenance strategies and optimized operational practices.
- Skill-Based Workforce Allocation: Assign personnel based on expertise to critical tasks, fostering innovation and effectiveness in core areas.
Implement Quality Control Measures
Embedding effective quality control measures throughout the additive manufacturing process is essential for ensuring product reliability and meeting customer expectations. Utilizing advanced monitoring systems and analytics is crucial for detecting potential issues and maintaining high quality standards. By integrating quality assurance practices at every stage, manufacturers can achieve reliable and consistent results.
Advanced Quality Control Practices:
- Real-Time Process Surveillance: Implement advanced sensor technologies to monitor production in real time and ensure adherence to specifications.
- Analytical Data Utilization: Leverage production data to identify patterns and implement preventative measures proactively.
- Conformity to Standards: Maintain alignment with industry standards to ensure uniformity and build credibility with clients.
Integrate with Traditional Manufacturing Processes
Strategically aligning additive manufacturing with existing production setups requires careful planning and execution. Overcoming integration challenges allows manufacturers to capitalize on the strengths of both additive and traditional methods. This hybrid approach enhances overall production capabilities and expands operational flexibility, catering to diverse market needs.
Effective Integration Techniques:
- Harmonized Process Coordination: Synchronize additive and conventional manufacturing processes to ensure smooth transitions and minimize operational disruptions.
- Material Synergy: Assess interactions between materials used in different manufacturing methods to ensure compatibility and quality.
- Collaborative Cross-Departmental Initiatives: Encourage cooperation across departments to leverage varied expertise and drive innovation throughout the production continuum.
Leverage Technology for Process Optimization
The strategic application of advanced technologies is integral to refining additive manufacturing processes. Automation, specialized software, and data-driven approaches contribute significantly to increasing production efficiency and fostering continuous enhancement. Embracing these technologies enables manufacturers to remain competitive and responsive to evolving market demands.
Technological Optimization Strategies:
- Process Automation: Introduce automated systems for routine tasks to allocate resources towards strategic development.
- Specialized Software Applications: Deploy software solutions for process modeling, simulation, and real-time performance tracking.
- Fostering Innovation: Cultivate a culture that encourages the exploration of emerging technologies and methodologies for ongoing process improvement.
Step 1: Establish a Comprehensive Workflow
Launching a detailed workflow in additive manufacturing demands a structured plan that accommodates the sophisticated nature of 3D printing. Constructing a strategic production framework is vital—ensuring every aspect of the operation integrates seamlessly. This strategic approach should meticulously detail each production phase, from initial design considerations to post-production analysis, facilitating a fluid transition throughout the manufacturing process.
Core Aspects of a Structured Workflow:
- Innovative Design Strategy: Focus on leveraging the distinctive advantages of additive manufacturing, such as complex geometries and reduced material usage. Employ advanced modeling tools that support iterative design improvements and validate concepts before manufacturing begins.
- Unified Production Planning: Develop a cohesive planning system that synchronizes all production-related functions. This integration enhances cross-departmental communication, ensuring that design, fabrication, and quality assurance teams collaborate effectively.
- Resource Optimization Framework: Establish a system for strategic resource planning that maximizes the utilization of materials, workforce, and machinery. This ensures optimal resource deployment, minimizing waste and controlling production costs.
Adopting Advanced Workflow Management Solutions:
The integration of specialized management solutions is essential for handling the intricacies of additive manufacturing. These solutions offer capabilities that streamline routine operations, monitor project development, and deliver real-time insights. Utilizing such solutions boosts operational efficiency and allows for agile adjustments to production schedules in response to immediate needs.
Advantages of a Well-Configured Workflow:
- Increased Operational Throughput: A well-configured workflow eliminates inefficiencies, accelerates production timelines, and reduces delays. This operational agility enables faster market entry for products, strengthening competitive positioning.
- Reliability in Production Quality: By standardizing operations and maintaining adherence to exacting standards, a structured workflow ensures reliability in production quality across different manufacturing cycles. This reliability enhances client trust and supports sustained business growth.
- Enhanced Agility and Responsiveness: A robust workflow empowers manufacturers to adapt swiftly to evolving design specifications or market conditions. This flexibility is crucial in the dynamic field of additive manufacturing, where customization and innovation drive success.
Step 2: Optimize Resource Allocation
Maximizing resource efficiency is critical in additive manufacturing, shaping the foundation for successful operations. Precise identification and strategic utilization of essential resources drive productivity and control costs. This involves a detailed understanding of material requisites, machine capabilities, and workforce strengths, ensuring alignment with production objectives.
Identifying and Utilizing Core Resources:
- Material Strategy: Develop a clear understanding of material needs, focusing on procurement efficiency and minimizing excess inventory. Accurate material forecasting helps avoid shortages and overstock, aligning supply with production demand.
- Equipment Optimization: Conduct thorough assessments of machinery to identify optimal usage patterns. Schedule operations to ensure machines run at high productivity levels, thus enhancing output and reducing idle periods.
- Skill-Based Allocation: Assign tasks based on individual expertise, ensuring that personnel are deployed where they can deliver maximum value. This approach not only improves output quality but also encourages skill development and innovation.
Strategies for Equitable Workload Distribution and Machine Utilization:
Equitable workload distribution ensures that all production resources are used efficiently, maintaining operational balance. This involves implementing systems that dynamically adjust to changing production demands and schedules.
- Adaptive Scheduling Systems: Introduce systems that adjust resource allocation in response to real-time production data. This adaptability ensures resources are efficiently used, aligning production capacity with demand.
- Proactive Equipment Maintenance: Implement systems that predict machine maintenance needs, addressing potential issues before they arise. This proactive approach minimizes disruptions and extends equipment lifespan.
- Comprehensive Capacity Assessment: Evaluate production capacity regularly to ensure alignment with current and future production needs. This assessment helps prevent resource bottlenecks and supports consistent production flow.
The Role of Advanced Manufacturing Execution Systems in Resource Optimization:
Advanced manufacturing execution systems (MES) serve as the backbone for effective resource management, integrating various operational aspects into a cohesive whole. These systems offer a centralized platform for real-time data access, enhancing decision-making and operational oversight.
- Comprehensive Data Integration: An MES facilitates comprehensive data integration, providing insights that inform strategic resource allocation. This integration enables manufacturers to adjust operations swiftly in response to shifting priorities.
- Real-Time Adjustment Capabilities: Monitor production metrics continuously to allow for immediate operational adjustments, ensuring efficient use of resources without compromising quality.
- Enhanced Cross-Functional Collaboration: Provide a unified platform for information sharing across departments, promoting synergy and alignment with production goals, leading to optimized resource utilization.
By focusing on the strategic deployment of materials, machinery, and personnel, manufacturers can achieve high levels of efficiency and innovation in additive manufacturing operations.
Step 3: Implement Quality Control Measures
In additive manufacturing, establishing a rigorous approach to quality assurance is essential to ensure product excellence. The focus should be on embedding systematic inspection protocols and leveraging advanced monitoring techniques across all production stages. This proactive stance not only maintains the integrity of the manufactured parts but also enhances operational credibility and customer satisfaction.
Techniques for Monitoring and Maintaining Quality in AM Processes
To achieve high-quality outcomes in additive manufacturing, it is crucial to utilize a combination of cutting-edge monitoring technologies and precise inspection methodologies. Advanced real-time monitoring tools are indispensable, providing continuous oversight of the manufacturing environment and enabling immediate interventions.
- Advanced Sensor Integration: Employ state-of-the-art sensors that continuously assess critical parameters such as temperature and deposition rates. These sensors facilitate rapid identification of deviations, allowing for timely corrective actions to uphold production standards.
- Precision Measurement Technologies: Utilize sophisticated measurement systems, including laser scanning and coordinate measuring machines (CMM), to ensure parts adhere to exact design specifications. This precision is vital for maintaining functional performance and meeting stringent tolerance requirements.
- Surface Quality Evaluation: Implement high-resolution imaging and surface profilometry to assess the finish of manufactured components. This evaluation helps identify surface inconsistencies that could impact product performance or appearance.
Utilizing Data Analytics for Continuous Improvement
Harnessing the power of data analytics is instrumental in refining quality control processes within additive manufacturing. By analyzing production data, manufacturers can extract actionable insights that drive process enhancements and foster a culture of continuous improvement.
- Comprehensive Pattern Recognition: Examine historical production data to uncover trends and correlations in quality metrics. This analysis provides a deeper understanding of factors influencing quality, guiding strategic process adjustments.
- Proactive Maintenance Strategies: Utilize predictive models to anticipate equipment maintenance needs and potential quality issues. This foresight enables planned interventions, minimizing disruptions and ensuring consistent quality.
- Iterative Feedback Systems: Develop feedback mechanisms that incorporate data from completed production runs to inform future process refinements. This iterative approach promotes ongoing optimization, ensuring that quality standards evolve with production advancements.
By embedding advanced quality control measures and leveraging data-driven insights, manufacturers can significantly elevate the reliability and excellence of their additive manufacturing operations.
Step 4: Integrate with Traditional Manufacturing Processes
Successfully merging additive manufacturing with traditional production lines requires a nuanced understanding of both methodologies. This integration leverages the distinct advantages of each approach, necessitating a strategic alignment that enhances operational efficiency and expands capabilities.
Strategies for Aligning Additive Manufacturing with Existing Production Lines
Effectively incorporating additive manufacturing into existing operations demands innovative solutions that bridge the gap between traditional and modern techniques. This alignment is crucial for optimizing production flow and unlocking new possibilities.
- Coordinated Workflow Development: Establish workflows that integrate additive manufacturing at strategic points where its unique capabilities—such as complex geometries and rapid prototyping—offer the most value. This integration should enhance, rather than disrupt, existing processes.
- Synergistic Team Dynamics: Develop interdisciplinary teams that combine expertise from both manufacturing domains. This collaboration fosters a shared understanding of production goals and encourages the development of integrated solutions that optimize resource use.
- Flexible Manufacturing Cells: Design production cells that can accommodate both additive and traditional manufacturing tasks, allowing seamless transitions and maximizing production agility. These cells facilitate rapid reconfiguration to meet changing demands.
Overcoming Challenges in Additive Manufacturing Integration with Conventional Methods
Merging these two manufacturing methodologies introduces several challenges, requiring innovative solutions and a willingness to adapt.
- Harmonizing Equipment and Materials: Develop solutions that ensure compatibility between additive technologies and traditional equipment. This may involve customizing interfaces or innovative tooling strategies to harmonize the two systems.
- Cultural Adaptation: Promote a culture that values adaptability and innovation, essential for integrating new technologies. Encourage a mindset where both traditional and additive methods coexist, fostering continuous improvement.
- Skill Enhancement Initiatives: Implement comprehensive training programs that equip the workforce with the skills necessary for operating both additive and traditional equipment. This dual expertise enhances operational capability and innovation potential.
Enhancing Workflow Management in Hybrid Manufacturing Environments
Creating a cohesive workflow in a hybrid manufacturing environment is critical for maintaining consistent output and quality.
- Unified Production Management Systems: Invest in cutting-edge software that centralizes management of both manufacturing processes. These systems provide real-time insights, enabling strategic decision-making and efficient resource allocation.
- Dynamic Process Evolution: Establish a continuous improvement framework that regularly assesses and refines hybrid workflows. This proactive approach ensures that integration remains effective and responsive to emerging challenges.
- Adaptive Production Framework: Design workflows that are inherently scalable and flexible to accommodate shifts in market demand or product specifications. This adaptability ensures resilience and competitiveness in a fluctuating market landscape.
Step 5: Leverage Technology for Process Optimization
Harnessing advanced technologies in additive manufacturing is essential for achieving precision and efficiency. These technologies enable detailed control over complex processes, paving the way for significant enhancements in both productivity and quality. By integrating innovations such as algorithmic optimization, simulation tools, and comprehensive data systems, manufacturers can realize transformative improvements in their workflows.
Advanced Technological Integration
The integration of sophisticated technologies into additive manufacturing processes facilitates the realization of operational excellence. By adopting these tools, manufacturers can streamline operations and ensure that their production strategies align with contemporary industry standards.
- Algorithmic Optimization: Utilize algorithm-based solutions to refine production parameters, ensuring optimal resource utilization and minimizing waste. These algorithms analyze complex datasets to recommend adjustments that enhance efficiency and output quality.
- Simulation and Modeling Tools: Employ advanced simulation software to model production scenarios and predict outcomes. This proactive approach allows manufacturers to identify potential bottlenecks and optimize processes before physical production begins.
- Comprehensive Data Systems: Develop integrated data systems that consolidate information from various production stages, enabling a holistic view of operations. This integration supports informed decision-making and strategic adjustments.
Automation and Software Enhancements
The strategic deployment of automation and software solutions is pivotal in optimizing production efficiency in additive manufacturing. These solutions reduce manual intervention and provide the flexibility needed to adapt to dynamic production requirements.
- Dynamic Workflow Automation: Implement systems that automate task scheduling and resource allocation, allowing for agile responses to changing demands. This automation ensures that production remains efficient and aligned with strategic objectives.
- Advanced Quality Assurance Systems: Introduce software that facilitates comprehensive quality assessments throughout the production cycle. These systems use real-time data to identify deviations and initiate corrective actions promptly.
- Maintenance and Reliability Tools: Adopt tools that predict maintenance needs and optimize equipment performance. These tools reduce unexpected downtimes and enhance machine reliability.
Continuous Improvement and Innovation
Fostering a culture of ongoing innovation is crucial for sustaining competitive advantage in additive manufacturing. By embracing forward-thinking strategies and cutting-edge technologies, manufacturers can maintain a trajectory of continuous improvement.
- Collaborative Innovation Networks: Establish networks that promote exchange of insights among industry stakeholders, driving collective problem-solving and innovation. These networks accelerate the development of advanced manufacturing solutions.
- Agility in Process Development: Implement agile methodologies that enable rapid adaptations to evolving market and technological landscapes. This flexibility supports sustained innovation and operational excellence.
- Feedback-Driven Process Evolution: Create mechanisms that capture and analyze feedback from production runs, informing strategic refinements. This iterative approach ensures that manufacturing processes evolve in line with industry advancements and customer expectations.
By leveraging these technological advancements, manufacturers can significantly enhance their additive manufacturing operations, ensuring sustained growth and productivity.
Final Thoughts
In the evolving landscape of industrial production, additive manufacturing stands as a testament to the power of innovation. The process planning and control of this technology demand a strategic approach that marries advanced methodologies with practical execution. Each step—from establishing a comprehensive workflow to leveraging cutting-edge technologies—contributes to a holistic framework that supports operational excellence.
The potential of additive manufacturing extends beyond mere integration with traditional methods; it heralds a new era of production flexibility and customization. By harnessing the unique capabilities of additive techniques, manufacturers can tailor products with unprecedented precision and complexity. This shift not only enhances the ability to meet specific market demands but also positions manufacturers at the forefront of innovation.
Continuous engagement with technological advancements propels the momentum for process optimization. The focus should be on developing adaptive systems that leverage real-time data to refine operations and anticipate future needs. By incorporating predictive analytics and machine learning, manufacturers can enhance their capacity to adapt swiftly to market changes, ensuring their operations remain resilient and forward-thinking.
As manufacturers navigate the intricacies of additive manufacturing, the emphasis must be on cultivating a culture of innovation and adaptability. By prioritizing strategic foresight and investing in transformative technologies, manufacturers can consistently deliver high-quality products. This commitment to excellence and continuous improvement will be the hallmark of those who lead the charge in tomorrow's dynamic manufacturing industry.
As you navigate the complexities of additive manufacturing process planning and control, remember that embracing innovation and leveraging advanced technologies are key to unlocking operational excellence. We at Phasio are committed to empowering manufacturers with cutting-edge solutions that streamline workflows, optimize resources, and drive continuous improvement. If you're ready to take your additive manufacturing operations to the next level, schedule a demo or try the platform to experience its capabilities and let us help you harness the full potential of this transformative technology.