The Importance of MES in Modern Manufacturing
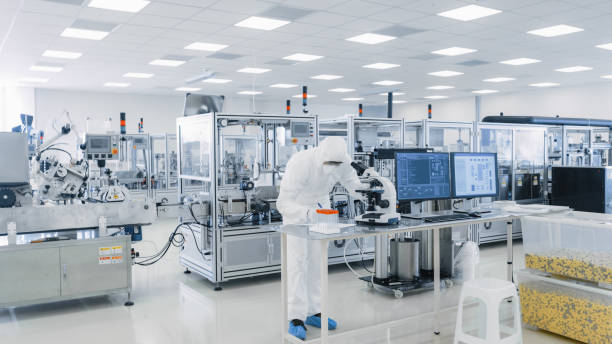
In today's fast-paced manufacturing landscape, businesses are constantly seeking ways to optimize their operations and stay ahead of the competition. To achieve this goal, many manufacturers are turning to advanced software solutions that can streamline their processes, improve visibility, and enhance overall efficiency.
One such solution that has gained significant traction in recent years is Manufacturing Execution Software (MES). By bridging the gap between enterprise-level systems and shop floor operations, MES has become an indispensable tool for manufacturers looking to take their production to the next level.
As the manufacturing industry continues to evolve, understanding the capabilities and benefits of MES is crucial for businesses aiming to remain competitive and meet the ever-changing demands of their customers.
What is Manufacturing Execution Software (MES)?
Manufacturing Execution Software (MES) is a comprehensive system designed to monitor, track, document, and control the entire manufacturing process — from raw materials to finished goods. By providing real-time visibility into production processes, MES enables manufacturers to optimize their output and efficiency, ensuring that they can meet their production targets while maintaining the highest levels of quality.
MES acts as an intermediate layer between Enterprise Resource Planning (ERP) systems and process control systems, effectively bridging the gap between business and production. This integration allows for seamless communication and data exchange between different levels of the organization, enabling better decision-making and more efficient resource allocation.
One of the key functions of MES is to create an "as-built" record of the manufacturing process. By capturing data and outcomes at every stage of production, MES provides a detailed and accurate account of how products are made. This information is particularly critical for industries with strict regulatory requirements, such as food and beverage or pharmaceutical, where traceability and compliance are paramount.
Real-time Production Monitoring and Control
MES empowers manufacturers with real-time monitoring capabilities, allowing them to keep a close eye on every aspect of their production processes. By collecting data from various sources, such as sensors, machines, and operators, MES provides a comprehensive view of the shop floor at any given moment. This real-time visibility enables manufacturers to quickly identify and address any issues that may arise, minimizing downtime and ensuring that production remains on track.
Optimizing Manufacturing Processes
With the insights gained from real-time monitoring, MES helps manufacturers optimize their processes for maximum efficiency. By analyzing production data, identifying bottlenecks, and pinpointing areas for improvement, MES enables manufacturers to make data-driven decisions that can significantly enhance their operations. This optimization can lead to reduced waste, improved resource utilization, and increased overall equipment effectiveness (OEE).
Bridging the Gap between ERP and Process Control
MES serves as a critical link between high-level business systems, such as ERP, and the low-level process control systems that directly manage production equipment. By integrating these systems, MES ensures that production aligns with business objectives and that the data generated on the shop floor is accessible and actionable at the enterprise level. This integration helps to break down silos within the organization, fostering better communication and collaboration between different departments.
Ensuring Regulatory Compliance and Traceability
For many industries, compliance with regulatory standards is a top priority. MES plays a vital role in ensuring that manufacturers meet these requirements by providing a complete and auditable record of the production process. By capturing data at every stage, from raw material intake to final product packaging, MES creates a detailed genealogy of each product. This traceability is essential for industries such as food and beverage or pharmaceutical, where the ability to quickly identify and recall products is critical to consumer safety.
Key Benefits of Implementing MES
Adopting a Manufacturing Execution Software (MES) system brings transformative enhancements to quality control within manufacturing operations. By facilitating precise process management, MES enables manufacturers to maintain stringent quality standards, reducing defects and ensuring consistency across production lines. This commitment to quality not only enhances product reliability but also boosts customer confidence, as products consistently meet exacting specifications.
MES significantly contributes to reducing downtime by enhancing production scheduling. Utilizing advanced analytics, MES allows for predictive adjustments in resource allocation, ensuring that machinery and personnel are optimally deployed. This proactive approach mitigates potential disruptions, ensuring that production maintains a steady flow and maximizing productivity across the board.
In the realm of inventory management, MES excels at streamlining operations by enhancing the accuracy and efficiency of material tracking. By providing comprehensive insights into inventory levels and usage patterns, manufacturers can align procurement processes more closely with production needs. This strategic alignment reduces excess inventory and associated carrying costs while minimizing the likelihood of shortages that can interrupt operations.
Moreover, MES supports the transition to digital shop floor operations, reducing reliance on paper-based processes. By integrating digital workflows, MES minimizes errors associated with manual data entry and enhances the speed and accuracy of data-driven decisions. This transition not only fosters operational efficiency but also aligns with sustainability goals by reducing paper consumption and waste. Through these digitized processes, manufacturers can also leverage cutting-edge technologies to continuously refine and enhance their operational strategies.
Core Features of Modern MES Solutions
Modern Manufacturing Execution Software (MES) solutions are equipped with a suite of features designed to meet the dynamic demands of today's manufacturing environments. These tools enhance operational efficiency, ensure product quality, and facilitate seamless integration across production systems.
Product Definition Management
Central to efficient manufacturing is the precise management of product specifications. Advanced MES systems offer robust capabilities for managing and updating master data such as production rules, bills of materials, and process set points. This ensures that all production stakeholders have access to the latest information, reducing the risk of errors and streamlining the planning process.
Resource Management and Scheduling
Effective resource allocation remains crucial for operational success. MES systems enhance this by providing sophisticated scheduling tools that align personnel, materials, and equipment with production demands. By leveraging these capabilities, manufacturers can maintain optimal production schedules, minimizing downtime and adjusting swiftly to changes in production requirements.
Production Execution and Monitoring
Executing production orders with precision requires constant oversight and adaptability. MES facilitates this through real-time management of production tasks, ensuring resources are utilized effectively. By continuously collecting and analyzing production data, MES identifies inefficiencies, paving the way for targeted improvements and maintaining a streamlined production flow.
Quality Management and Compliance
In industries where quality and compliance are critical, MES acts as a cornerstone for maintaining standards. The software systematically tracks quality metrics, promptly identifying deviations to uphold product integrity. Furthermore, MES provides detailed traceability of the manufacturing process, ensuring that all products meet necessary compliance standards and can be audited with ease.
Integrating MES with Other Manufacturing Systems
In the competitive landscape of modern manufacturing, the integration of Manufacturing Execution Software (MES) with other systems represents a strategic advantage. This connectivity ensures that production activities are not isolated but rather intertwined with the broader operational framework of the organization. A critical integration point is with Customer Relationship Management (CRM) systems, which enhances the ability to track customer interactions and feedback, thus aligning production more closely with customer demands and improving service delivery.
Additionally, MES extends its integration capabilities to specialized workflow systems that drive efficiency and precision in operations. By interfacing with Laboratory Information Management Systems (LIMS), MES ensures that quality control processes are seamlessly integrated with production, providing real-time insights into material and product quality. Similarly, integration with Warehouse Management Systems (WMS) allows for the dynamic management of inventory, ensuring that materials are available just in time for production, thus reducing holding costs and optimizing supply chain efficiency.
Furthermore, MES plays a pivotal role in integrating with cutting-edge technologies such as Internet of Things (IoT) platforms and data analytics tools. This integration facilitates the collection and analysis of data from various production sources, enabling predictive maintenance and real-time decision-making. By leveraging these technologies, manufacturers can enhance process visibility and agility, adapting swiftly to market changes while maintaining high standards of product quality and consistency.
Leveraging MES for Smart Manufacturing and Industry 4.0
Incorporating Manufacturing Execution Software (MES) into manufacturing processes is a significant step toward achieving the smart manufacturing goals of Industry 4.0. It offers unprecedented transparency by delivering comprehensive insights into production activities. This transparency ensures swift adaptation to production variables, enhancing operational effectiveness and product consistency.
MES's capacity for integration extends to advanced data-driven technologies, including Industrial Internet of Things (IIoT) devices, which collect extensive operational data. This data, when processed by machine learning algorithms, provides actionable insights into production trends and potential inefficiencies. By leveraging these insights, manufacturers can refine their production strategies, anticipate equipment needs, and implement proactive adjustments to maintain optimal performance.
The shift toward mass customization demands a manufacturing infrastructure that supports agile production methods. MES is integral to this shift, offering the flexibility required to accommodate diverse product specifications and rapid order changes. By providing manufacturers with detailed, real-time production metrics, MES empowers them to execute seamless transitions in production lines, thus meeting varied consumer demands effectively. This adaptability is central to driving digital transformation, positioning manufacturers at the forefront of innovation and competitiveness in the industry.
Implementing MES: Best Practices and Considerations
The implementation of a Manufacturing Execution Software (MES) system requires a strategic approach to ensure it delivers the intended benefits. A thorough assessment of current manufacturing processes is the first step. This involves mapping out existing workflows and pinpointing inefficiencies or bottlenecks that hinder productivity. Such an evaluation allows for the customization of the MES to address these specific challenges, ensuring that the system's deployment leads to significant operational enhancements.
Defining clear objectives and key performance indicators (KPIs) is essential for measuring the success of the MES implementation. These objectives should be aligned with overarching business strategies, aiming to improve metrics like yield rates, cycle times, or defect rates. Establishing well-defined KPIs provides a benchmark for performance evaluation, enabling organizations to track progress and make adjustments as needed. This structured approach ensures that the MES contributes effectively to achieving the company's manufacturing goals.
Aligning MES with other technological investments is crucial for optimizing its effectiveness. This not only involves technical integration but also aligning MES functionalities with existing business processes, ensuring that it complements and enhances current operations. By creating a unified digital environment, manufacturers can achieve greater coherence across their operations, facilitating smoother transitions and more informed decision-making at all levels of production.
Ensuring that staff are well-equipped to utilize the MES is another critical component of a successful implementation. Tailored training programs should focus on building competency in using the system's features to their fullest potential. By fostering a proactive learning culture, employees become adept at navigating new tools and processes, leading to improved efficiency and reduced resistance to change. This empowerment of the workforce ensures that they can fully exploit the MES's capabilities.
To sustain the benefits of an MES, continuous monitoring of its performance is necessary. This involves regularly assessing system outputs and user feedback to identify opportunities for enhancement. Implementing a dynamic feedback loop allows for agile adjustments, ensuring that the MES adapts to evolving production needs and continues to drive improvements. This commitment to ongoing refinement not only maximizes the return on investment but also keeps the organization agile and competitive in an ever-changing manufacturing landscape.
As the manufacturing landscape continues to evolve, embracing advanced solutions like Manufacturing Execution Software (MES) is no longer optional — it's a necessity for businesses that want to thrive in the era of Industry 4.0. At Phasio, we understand the challenges manufacturers face and have developed a cutting-edge platform to help you streamline your operations, improve efficiency, and drive growth. If you're ready to take your manufacturing to the next level, schedule a demo or try the platform to experience its capabilities firsthand and see how we can help you achieve your goals.