Evaluating MES Solutions for Enhanced MJF Performance
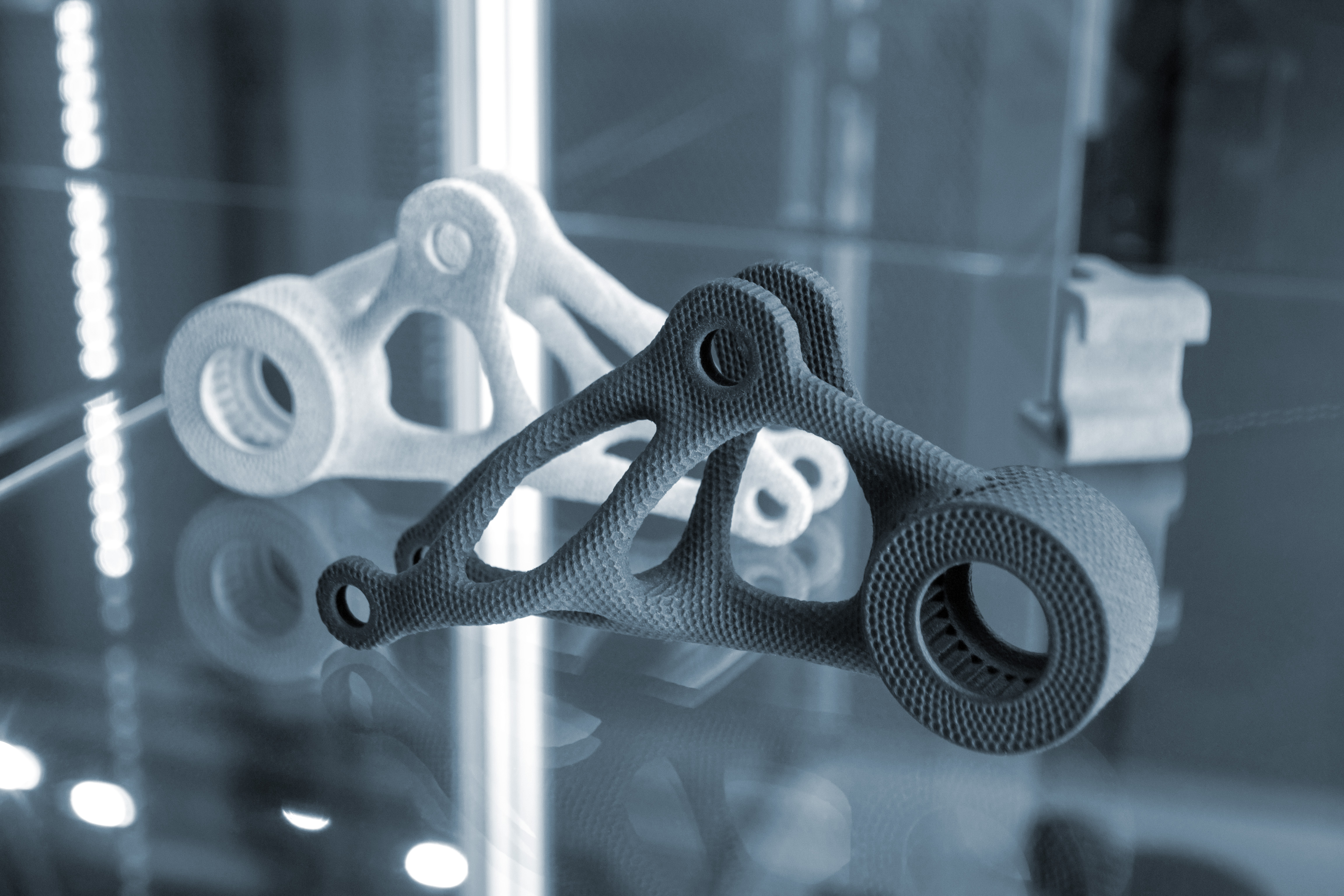
In today's fast-paced manufacturing landscape, companies are constantly seeking ways to optimize their production processes and stay ahead of the competition. One technology that has gained significant traction in recent years is Multi Jet Fusion (MJF), a powerful 3D printing method that enables the creation of complex, high-quality parts with unparalleled speed and precision.
However, to truly harness the potential of MJF and streamline operations, manufacturers need a robust system that can monitor, control, and analyze every aspect of the production process. This is where a Manufacturing Execution System (MES) comes into play.
By implementing an MES tailored specifically for MJF, manufacturers can unlock new levels of efficiency, quality, and profitability in their additive manufacturing operations. Let's explore the concept of MES and its crucial role in optimizing MJF production. We invite you to explore how our cutting-edge solutions can transform your manufacturing operations and propel your business to new heights. Schedule a demo or try the platform to experience its capabilities and let us help you unlock the full potential of your MJF production.
What is a Manufacturing Execution System (MES)?
A Manufacturing Execution System (MES) is a comprehensive software solution designed to monitor, track, document, and control the entire manufacturing process from raw materials to finished products. It serves as a functional layer between Enterprise Resource Planning (ERP) systems and process control systems, providing decision-makers with real-time data to improve plant floor efficiency.
In the context of Multi Jet Fusion, an MES is particularly essential for driving optimal performance in today's competitive and rapidly changing manufacturing environment. MJF technology offers unparalleled speed, precision, and design freedom, but to fully capitalize on these benefits, manufacturers need a system that can seamlessly integrate with their MJF workflows and provide real-time visibility into every aspect of the production process.
An MES designed for MJF enables manufacturers to:
- Monitor production in real-time: Collect and analyze data from MJF printers, post-processing equipment, and quality control checkpoints to gain a comprehensive view of the production process.
- Optimize resource allocation: Leverage sophisticated scheduling algorithms to ensure that MJF operations are executed at the right time with the appropriate assets, minimizing downtime and maximizing efficiency.
- Ensure quality and traceability: Implement statistical process control (SPC) and defect tracking to maintain the highest product quality standards while providing complete traceability for compliance and regulatory purposes.
By implementing an MES that seamlessly integrates with MJF workflows, manufacturers can unlock new levels of efficiency, quality, and profitability in their additive manufacturing operations. The system enables real-time monitoring and control of MJF printers, post-processing stations, and quality control checkpoints while facilitating data exchange with other critical systems such as ERP, Product Lifecycle Management (PLM), and quality management software.
When selecting an MES for MJF production, it's crucial to consider factors such as scalability, flexibility, and vendor experience. The ideal MES should be able to adapt to changing production needs, scale as MJF operations grow, and support the integration of new technologies and processes. Additionally, evaluating the vendor's experience in implementing MES in MJF and additive manufacturing environments, as well as the quality of their training, support, and professional services, can ensure a successful deployment.
Implementing an MES to optimize MJF production requires careful planning and collaboration across various functions, including manufacturing, quality, IT, and business. Developing a phased implementation plan aligned with key MJF production goals and metrics, establishing a governance model, and driving continuous improvement leveraging MES data and insights are all critical components of a successful MES deployment.
Ultimately, an MES empowers manufacturers to harness the full potential of MJF technology, enabling them to innovate, optimize, and scale their additive manufacturing operations. By leveraging the real-time data and insights provided by an MES, manufacturers can identify opportunities for process improvement, support new product introduction, and empower their workforce to achieve new levels of efficiency and quality in MJF production.
Key Features and Benefits of MES for MJF
Real-time Production Monitoring
Incorporating cutting-edge technology, an MES for Multi Jet Fusion revolutionizes production oversight by delivering instantaneous visibility into manufacturing operations. This system taps into machine data, sensor inputs, and operator feedback, assembling a cohesive snapshot of the production environment. With these insights, manufacturers can systematically uncover operational bottlenecks and streamline production phases, leveraging data to refine processes and enhance overall efficiency.
An MES transforms this data into actionable intelligence, allowing manufacturers to make precise adjustments to their operations. By continuously monitoring performance metrics, the system not only identifies potential disruptions but also enhances decision-making capabilities, ensuring that production maintains optimal momentum and output quality.
Optimized Resource Allocation
Resource allocation within a Multi Jet Fusion environment demands precision and foresight, a task adeptly handled by an MES through its advanced scheduling capabilities. The system allocates tasks and resources with pinpoint accuracy, ensuring that production sequences are executed seamlessly and without interruptions. Such meticulous planning guarantees that all operations utilize assets effectively, achieving high throughput without sacrificing quality.
Strategic resource management is about more than just timing; it's about maximizing asset efficiency. The MES facilitates this by dynamically adjusting resource deployment to align with production goals, helping manufacturers meet stringent deadlines and maintain quality standards. This approach ensures a harmonious balance between operational efficiency and product excellence.
Quality Management and Traceability
In the realm of MJF, maintaining impeccable quality is paramount, and an MES serves as a critical tool in this endeavor. It provides robust mechanisms for monitoring quality through real-time analytics, ensuring that each part produced adheres to exacting standards. By minimizing defects and reducing rework, the system preserves both resources and time, fostering an environment of continuous improvement.
The MES also enhances traceability by offering comprehensive tracking of each product's journey through the manufacturing process. This capability not only ensures compliance with regulatory standards but also builds transparency and trust. Manufacturers can swiftly trace and address any discrepancies, thereby maintaining the integrity of their production lines and reinforcing customer confidence.
Integrating MES with MJF Workflows
Integrating a Manufacturing Execution System with MJF workflows requires a nuanced approach that respects the intricacies of both the MES platform and the MJF technology it supports. The integration ensures that MJF production processes operate with heightened precision and coordination. An effective MES provides a synchronized framework, orchestrating the operations of MJF printers, post-processing stages, and quality assurance checkpoints, thereby enhancing operational visibility and keeping production aligned with strategic goals.
The integration process involves creating a seamless connection between various systems, allowing for fluid data transfer and operational cohesion. Beyond the immediate production environment, this integration encompasses broader enterprise systems, facilitating comprehensive oversight across supply chain management and production planning. By establishing a reliable data interchange, the MES empowers manufacturers to streamline production schedules, optimize resource deployment, and ensure consistent quality control, thereby fostering harmonious operations across the entire MJF workflow.
To fully realize the benefits of MES integration, manufacturers must carefully evaluate their existing infrastructure and identify potential areas for enhancement. This may involve upgrading equipment or implementing new protocols to support seamless data transfer and system interoperability. Key considerations include ensuring that the MES can evolve alongside the organization's growth and adapt to new technologies and processes.
A successful MES integration not only optimizes current manufacturing capabilities but also positions manufacturers to adapt swiftly to industry changes and emerging opportunities. By building a robust, interconnected ecosystem, organizations can drive innovation, enhance productivity, and maintain a competitive edge in the rapidly evolving landscape of Multi Jet Fusion technology.
Selecting the Right MES for MJF Production
Identifying the most suitable Manufacturing Execution System for Multi Jet Fusion involves a strategic approach that considers both immediate operational goals and future scalability. The chosen system must exhibit robust adaptability to embrace the ever-evolving landscape of MJF technology. This adaptability ensures that the MES remains an instrumental component in enhancing production workflows while accommodating the unique operational demands presented by the dynamic nature of additive manufacturing.
A critical aspect of this adaptability is the system’s ability to integrate emerging technologies and processes, ensuring seamless transitions as the industry progresses. Employing low-code platforms, the MES can be tailored to meet specific business needs, offering customized solutions that enhance responsiveness and efficiency. This capability ensures that the system not only manages existing tasks effectively but also scales to handle increased complexity and volume as operations expand.
The selection process must also weigh the vendor's expertise and the quality of their support infrastructure. It's essential to choose a vendor with a proven track record in MES implementations within the context of MJF and additive manufacturing. This experience indicates a nuanced understanding of industry-specific challenges, ensuring the system is designed for optimal performance. Comprehensive support services and training programs are vital, as they equip teams to leverage the system's full potential. Evaluating the vendor's vision for future advancements in MJF technology can provide insights into their commitment to innovation and long-term partnership.
Implementing MES to Optimize MJF Production
Optimizing MJF production through an MES requires a strategic approach that prioritizes clear objectives and adaptable processes. The initial step is to craft a detailed roadmap that aligns with the specific demands of Multi Jet Fusion technology. This roadmap should be segmented into actionable phases, each designed to tackle distinct operational challenges and leverage opportunities systematically. By doing so, the integration of MES becomes a targeted effort to enhance productivity and quality across all stages of production.
Active participation from key personnel across departments such as manufacturing, quality assurance, IT, and business operations is essential for tailoring the MES to meet organizational needs. Their insights and expertise are invaluable in customizing the system's features to optimize workflow and output. This collaborative effort ensures that the MES is not only implemented effectively but is also embraced by all users, fostering a culture of continuous improvement.
To ensure the MES delivers sustained benefits, a dynamic governance framework is vital. This framework should encompass flexible processes that allow for the seamless integration of MES insights into regular operations. By continuously analyzing data, the organization can identify and address inefficiencies promptly, maintaining a cycle of ongoing enhancement. This proactive approach enables the MES to serve as a driving force for innovation within Multi Jet Fusion production.
Regular assessments of MES performance are critical to understanding its impact on efficiency, quality, compliance, and costs. By systematically evaluating these metrics, the organization can gauge the effectiveness of the MES and make informed decisions for future improvements. This approach not only demonstrates the value of the MES but also informs strategic planning, ensuring the system remains a pivotal element in advancing MJF production capabilities.
Leveraging MES to Advance MJF Innovation
Implementing an MES offers unique opportunities to propel innovation in Multi Jet Fusion (MJF) production. By transforming operational observations into actionable strategies, the MES becomes a catalyst for identifying novel pathways to enhance and differentiate manufacturing processes. This strategic use of system data enables manufacturers to not only refine existing workflows but also explore pioneering techniques that push the boundaries of MJF capabilities.
A critical advantage of MES is its ability to streamline the introduction of new products through digital frameworks. By converting work instructions and best practices into digital formats, the MES ensures they are consistently applied across production cycles. This digital transformation reduces the likelihood of errors and accelerates the introduction process, ensuring new products reach the market swiftly while adhering to stringent quality benchmarks.
The MES also serves as an integrative platform that bridges the gap between MJF and conventional manufacturing methods. It establishes a cohesive operational environment where resource management and scheduling are optimized across different manufacturing modalities. This integration allows manufacturers to maintain flexibility and agility, adapting to technological advancements and shifting market demands with ease.
Empowering the workforce with precise operational insights is key to maximizing MES benefits. By equipping production teams with detailed guidance and real-time feedback, the MES fosters a proactive manufacturing culture. This empowerment encourages operators to make informed adjustments, implement process enhancements, and embrace a mindset geared towards continuous improvement and innovation. Such a dynamic approach not only elevates individual performance but also enhances the overall efficiency and effectiveness of the manufacturing operation.
As you embark on your journey to optimize MJF production, remember that the right MES can be a powerful ally in driving innovation, efficiency, and quality. We invite you to explore how our cutting-edge solutions can transform your manufacturing operations and propel your business to new heights. Schedule a demo or try the platform to experience its capabilities and let us help you unlock the full potential of your MJF production.