The Role of Multi-Process Manufacturing Software in Modern Industry
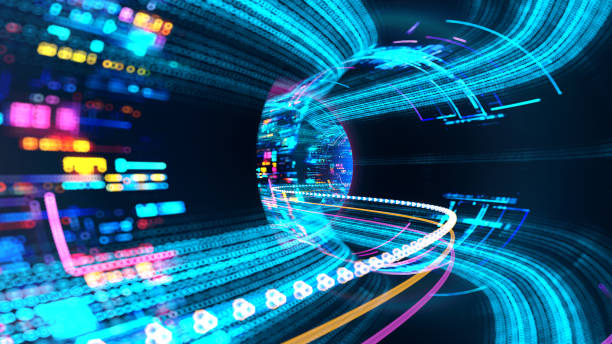
In today's fast-paced manufacturing landscape, companies face the challenge of managing diverse production processes while maintaining efficiency and competitiveness. As a result, many manufacturers are turning to advanced software solutions to streamline their operations and optimize their workflows.
Multi-process manufacturing software has emerged as a game-changer, empowering businesses to effectively manage and integrate various production methods within a single, comprehensive platform. By leveraging these cutting-edge tools, manufacturers can unlock new levels of productivity, quality, and agility.
In this article, we'll explore the world of multi-process manufacturing software, delving into its key features, benefits, and considerations for implementation. Whether you're a seasoned manufacturing professional or a business owner looking to optimize your operations, this guide will provide valuable insights to help you navigate the complex landscape of modern manufacturing technology.
What is Multi-Process Manufacturing Software?
Multi-process manufacturing software is a comprehensive solution designed to manage and optimize diverse production methods within a single, integrated platform. This powerful technology streamlines operations across various manufacturing processes, such as batch, continuous, and discrete, enabling manufacturers to efficiently manage resources, inventory, and production workflows.
One of the key advantages of multi-process manufacturing software is its ability to provide real-time visibility and control over the entire manufacturing lifecycle. By integrating different aspects of the manufacturing process — from raw materials to finished goods — these solutions facilitate seamless communication and collaboration between departments, ensuring that everyone is working towards a common goal.
Moreover, multi-process manufacturing software offers a range of features tailored to the unique needs of each manufacturing process. For example, batch manufacturing requires precise recipe management and scalability, while continuous manufacturing demands real-time monitoring and control. By accommodating these specific requirements within a single system, multi-process manufacturing software eliminates the need for multiple, disparate solutions, reducing complexity and enhancing overall efficiency.
In addition to streamlining operations, multi-process manufacturing software also plays a crucial role in ensuring product quality and compliance. With built-in quality control tools and traceability features, manufacturers can closely monitor production processes, identify potential issues, and take corrective actions promptly. This not only helps maintain consistent product quality but also facilitates compliance with industry regulations and standards.
As the manufacturing landscape continues to evolve, the adoption of multi-process manufacturing software has become increasingly essential for businesses looking to stay competitive. By leveraging the power of these advanced solutions, manufacturers can optimize their operations, reduce costs, and deliver high-quality products to their customers, all while navigating the complexities of modern manufacturing.
In the following sections, we'll explore the key benefits of implementing multi-process manufacturing software, as well as the essential features to look for when selecting a solution for your business. Whether you're a small-scale manufacturer or a large enterprise, understanding the capabilities and potential of multi-process manufacturing software is crucial to driving success in today's dynamic manufacturing environment.
Benefits of Implementing Multi-Process Manufacturing Software
Improved Efficiency and Productivity
By integrating a comprehensive multi-process manufacturing software, businesses can transform their operational landscape. This software automates intricate workflows, thereby reducing manual interventions and enhancing precision. The elimination of isolated data silos facilitates a unified data environment, driving accuracy and reducing operational errors. Furthermore, optimizing resource allocation leads to minimized waste and maximized profitability, creating a robust foundation for sustainable growth.
The software also fosters a seamless flow of information across departments, ensuring that every team operates with synchronized objectives. This interconnected framework empowers teams to act decisively, leveraging real-time insights to address challenges promptly. As a result, the organization experiences a significant boost in productivity, driven by enhanced collaboration and informed decision-making.
Enhanced Quality Control and Compliance
Advanced quality assurance becomes attainable with the implementation of multi-process manufacturing software. The system's capabilities in monitoring production processes in real-time ensure that each product meets the desired quality standards consistently. By providing dedicated modules for quality inspections, testing, and corrective measures, the software enables firms to maintain stringent quality benchmarks.
Maintaining compliance with industry-specific regulations becomes more straightforward, as the software integrates regulatory checks into the production workflow. This proactive approach to compliance reduces the risk of penalties and ensures that manufacturing operations align with legal requirements. Manufacturers benefit from a system that not only supports quality assurance but also reinforces compliance as a core operational element.
Increased Flexibility and Agility
Adapting to evolving market conditions is crucial, and multi-process manufacturing software offers the agility needed to thrive. It empowers manufacturers to swiftly pivot their strategies in response to changing customer demands and market trends. The system supports the rapid development and deployment of new products, facilitating a quicker entry into the market — a critical advantage in competitive industries.
Managing complex supply networks and multiple production sites becomes seamless with this software, as it provides the tools necessary for effective coordination and logistics management. Manufacturers can respond to fluctuations and challenges with agility, ensuring that operations remain resilient and responsive to new opportunities.
Key Features of Multi-Process Manufacturing Software
Unified Inventory Oversight
A standout feature of multi-process manufacturing software is its comprehensive approach to inventory oversight, effectively managing raw materials, work-in-progress items, and completed goods. This holistic system ensures optimal stock levels, significantly cutting down on excess inventory costs and preventing shortages. With clear, up-to-date inventory visuals, manufacturers can strategically plan production schedules to align with material availability, meeting consumer demands with precision.
Dynamic Production Planning and Scheduling
The software offers sophisticated production planning and scheduling tools, crucial for maximizing resource allocation. It supports agile scheduling that responds swiftly to live data, enabling manufacturers to deploy resources efficiently and reduce idle times. This feature is especially advantageous in multi-line production environments, ensuring smooth coordination of complex manufacturing tasks.
Robust Quality Assurance Systems
Multi-process manufacturing software excels in implementing robust quality assurance systems, equipping manufacturers with tools to uphold stringent quality standards. By incorporating comprehensive inspection, testing, and corrective modules, the software ensures product consistency and adherence to compliance requirements. This proactive quality management approach allows manufacturers to preemptively address potential quality issues throughout the production lifecycle.
Advanced Data Utilization and Insights
The software's capability for advanced data utilization and insights is vital for strategic decision-making and fostering continuous improvements. Through detailed analytics, manufacturers gain actionable insights into production efficiencies and operational performance, supporting informed strategic planning. This data-centric methodology enables the identification of improvement opportunities, optimizing processes and boosting overall productivity.
Enhanced Operational Control and Precision
Incorporating a Manufacturing Execution System (MES) within the software provides enhanced operational control and precision on the shop floor. MES capabilities offer granular insights into production activities, facilitating accurate monitoring and management of manufacturing processes. Additionally, integration with CNC machining systems refines production workflows, minimizing manual processes and enhancing machining precision.
Comprehensive Financial Oversight and Connectivity
The software includes extensive financial oversight tools, ensuring precise cost management and profitability analytics. These modules provide in-depth financial visibility, aiding manufacturers in budget management, cost analysis, and profitability optimization. Moreover, the software's seamless integration with other enterprise systems like ERP, CRM, and SCM fosters a unified operational framework, streamlining processes across the entire organization.
Choosing the Right Multi-Process Manufacturing Software
Assessing Your Unique Requirements
The journey to selecting the appropriate multi-process manufacturing software begins with a comprehensive evaluation of your organization's distinct needs. Every manufacturing operation is unique, influenced by its specific processes and challenges. Start by identifying these processes, pinpointing inefficiencies, and determining how the software can address them. It's essential to look beyond the present, considering scalability and flexibility to accommodate future growth.
Your current IT infrastructure and integration capabilities also require careful assessment. Understand how the new software will integrate with your existing systems to ensure seamless connectivity. By identifying integration points, you can select software that enhances your IT landscape, fostering a more cohesive operational environment.
Evaluating Software Features and Capabilities
When evaluating software options, prioritize solutions that offer robust features tailored to your industry and specific manufacturing needs. Comprehensive functionality is key, covering aspects such as production planning, quality control, and financial management. Focus on how these features align with your operational goals and support the intricacies of your manufacturing environment.
User experience and adoption are critical to successful implementation. Consider the software's interface and ease of use, ensuring it facilitates smooth adoption without major disruptions. Access to training resources and support services is equally important, empowering your team to fully utilize the software.
Integration capabilities are another crucial factor. The software should seamlessly connect with existing systems, providing end-to-end visibility and control. Evaluate how well the solution integrates with your technology stack, ensuring it complements your workflows without causing disruptions.
Selecting a Trusted Software Provider
Selecting a software provider involves researching their reputation and track record in the industry. Look for providers with a history of serving manufacturers similar to your own, focusing on their expertise and success stories. A provider with a strong industry presence can offer valuable insights and tailored solutions.
Evaluate the provider's support offerings, including customer service and ongoing product updates. A commitment to continuous improvement indicates the provider's dedication to evolving their software in line with industry advancements. This assurance is crucial for maintaining the software's effectiveness over time.
Finally, conduct a thorough cost analysis, considering both upfront and long-term costs. Factor in maintenance fees, potential upgrades, and the expected return on investment. A clear understanding of these financial aspects helps ensure the chosen software aligns with your strategic objectives.
Implementing and Leveraging Multi-Process Manufacturing Software
Crafting a strategic implementation plan forms the cornerstone of integrating multi-process manufacturing software into your operations. A well-defined timeline with specific milestones ensures that each phase of deployment progresses smoothly. It's essential to allocate resources judiciously, assembling a cross-functional team to oversee the process. This team should include representatives from key departments to provide diverse perspectives and ensure alignment with company goals.
Ensuring organizational alignment hinges on involving stakeholders from the outset. By engaging key personnel, you create a collaborative environment that encourages open communication and shared objectives. Clearly articulating the software's benefits and how it aligns with the company's strategic direction is critical. This transparency helps mitigate apprehensions and fosters a culture of acceptance and enthusiasm for the new system.
Training programs must be robust, focusing on empowering users with the necessary skills to utilize the software effectively. Tailored sessions that address specific user needs can enhance engagement and confidence. Continued support and accessible resources are vital for maintaining momentum and encouraging users to explore advanced features as their proficiency grows.
Performance metrics should be continuously monitored to gauge the software's impact on operations. By closely analyzing these insights, manufacturers can pinpoint inefficiencies and areas for enhancement. This proactive approach allows for timely interventions that refine processes and drive operational excellence. Regular reviews ensure that the software evolves in tandem with organizational needs, maintaining its role as a vital tool for growth.
The scope of multi-process manufacturing software extends beyond immediate operational benefits. By leveraging its capabilities, manufacturers can anticipate market trends and customer preferences, positioning themselves advantageously. The software's analytics and insights enable quick adjustments to strategies, supporting innovation and enhancing service delivery. Such responsiveness strengthens market presence and solidifies a competitive edge, fostering sustainable growth.
As the manufacturing landscape continues to evolve, embracing multi-process manufacturing software becomes a strategic imperative for businesses seeking to thrive in an increasingly competitive environment. By harnessing the power of these advanced solutions, manufacturers can unlock new levels of efficiency, agility, and innovation, positioning themselves for long-term success. If you're ready to transform your manufacturing operations and take your business to the next level, schedule a demo or try the platform to experience its capabilities firsthand — we're here to support you every step of the way.