Understanding Additive Manufacturing: A Comprehensive Guide
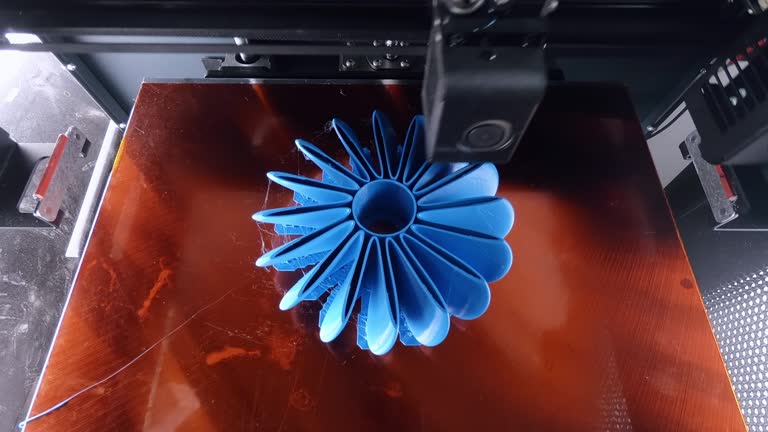
Additive manufacturing, or 3D printing, has revolutionized the way we create objects — from prototypes to end-use parts. This innovative process builds up components layer by layer, using materials like plastics, metals, and ceramics, guided by digital 3D design files.
Compared to traditional subtractive manufacturing methods such as machining or milling, additive manufacturing offers unparalleled flexibility and design freedom. Complex geometries that were once impossible to produce with conventional techniques can now be realized through 3D printing.
Additive manufacturing encompasses a wide range of technologies, each with its own unique capabilities and advantages. From fused deposition modeling (FDM) for thermoplastics to selective laser sintering (SLS) for metals and polymers, the options are vast and continually expanding.
What is Additive Manufacturing?
At its core, additive manufacturing is a process that creates three-dimensional objects by successively adding material in layers. This additive approach stands in stark contrast to traditional subtractive manufacturing methods, where material is removed through cutting, drilling, or milling to achieve the final shape.
One of the key enablers of additive manufacturing is the use of digital 3D design files, such as CAD models or 3D scans. These digital blueprints guide the 3D printer in precisely depositing or fusing material, layer by layer, to build up the desired object. This direct digital manufacturing approach eliminates the need for tooling and allows for rapid iteration and customization.
Additive manufacturing's ability to create complex geometries is a significant advantage over traditional manufacturing methods. Intricate internal structures, lattices, and organic shapes that would be difficult or impossible to produce through machining can be readily fabricated with 3D printing. This design freedom opens up new possibilities for lightweight components, optimized fluid flow channels, and patient-specific medical implants.
The additive manufacturing landscape is diverse, with various technologies catering to different materials and applications:
- Fused Deposition Modeling (FDM): Extrudes thermoplastic filament layer by layer to build up parts. Commonly used materials include ABS, PLA, and Nylon.
- Selective Laser Sintering (SLS): Uses a laser to sinter powdered materials like nylon, TPU, and metal composites into solid parts.
- Stereolithography (SLA): Employs a UV laser to cure and harden liquid photopolymer resin, creating highly detailed and smooth-surfaced parts.
- Direct Metal Laser Sintering (DMLS) and Selective Laser Melting (SLM): Use high-powered lasers to fuse metal powder into dense, strong metal parts. Popular materials include stainless steel, titanium, and aluminum.
- Electron Beam Melting (EBM): Similar to DMLS/SLM but uses an electron beam to melt metal powder, enabling the production of large, complex metal components.
- Binder Jetting: Deposits a liquid binding agent onto a powder bed to join particles together. Can be used with metals, sand, and ceramics.
These additive manufacturing technologies, each with their distinct capabilities and material compatibilities, have found applications across diverse industries — from aerospace and automotive to healthcare and consumer goods. The ability to rapidly produce prototypes, manufacture complex parts on-demand, and enable mass customization has made additive manufacturing an invaluable tool for businesses looking to streamline their operations and deliver innovative solutions to their customers, such as the services offered at Phasio.
As additive manufacturing continues to evolve and mature, we can expect to see faster build speeds, larger build volumes, and an ever-expanding range of materials. The integration of additive manufacturing execution systems, like those developed at Phasio, will further optimize workflows and streamline production processes. With its potential to transform supply chains, enable distributed manufacturing, and unlock new design possibilities, additive manufacturing is poised to play an increasingly vital role in the future of manufacturing.
How Does the Additive Manufacturing Process Work?
The journey begins with a precise digital model, often crafted using advanced CAD software or derived from a detailed 3D scan. This digital representation captures every nuance of the object, setting the stage for its physical manifestation. Specialized software then translates this model into distinct slices, each representing a single layer of the final object. This slicing process is pivotal—it dictates the printer's path, ensuring each layer aligns seamlessly.
Following slicing, the model is strategically positioned within the 3D printer's workspace. Proper orientation is crucial, influencing the mechanical properties and minimizing the necessity for additional structural supports. These supports are integral to maintaining stability during the build phase, particularly for intricate designs. Generated either automatically or manually, they facilitate the construction of complex geometries and are subsequently removed during the finishing stages.
The printing phase commences with the 3D printer executing the meticulously planned instructions. Employing materials such as thermoplastics, metal powders, or resins, the printer constructs the object layer by layer. Each material layer solidifies and adheres to the previous one, gradually forming the complete structure. This methodical process allows for the creation of intricate and robust designs that are challenging to achieve with conventional manufacturing methods.
Post-printing refinement is critical to achieving the desired quality and functionality of the printed object. Depending on the material and design complexity, this may include removing support structures, enhancing surface finishes, and applying specific treatments like heat curing or UV exposure. These steps ensure that the final product meets precise specifications and is ready for its intended application. This comprehensive approach underscores the versatility and precision of additive manufacturing, enabling the production of high-quality, custom parts across various industries.
Applications and Benefits of Additive Manufacturing
Additive manufacturing has become integral across diverse sectors, transforming traditional processes and introducing novel opportunities. A prominent application is the acceleration of product development through rapid prototyping. This capability allows designers and engineers to swiftly transition from concept to prototype, facilitating immediate testing and iteration. By significantly reducing the time and cost associated with traditional prototyping, companies can respond more dynamically to market demands and innovative ideas.
One of the most beneficial aspects of additive manufacturing is its ability to cater to customization on a massive scale. This is particularly impactful in fields requiring highly individualized solutions, such as personalized medical devices or tailored consumer products. The technology supports on-demand manufacturing, enabling businesses to efficiently produce items as required without the burden of excess inventory, effectively transforming the supply chain landscape.
Environmental and economic advantages are substantial; additive manufacturing constructs items by precisely adding material where needed, thus minimizing waste. This efficiency not only aligns with sustainability goals but also reduces production costs. Additionally, the technology enables decentralized production, allowing for localized manufacturing that reduces logistical expenses and shortens delivery timelines.
In industries like aerospace and automotive, additive manufacturing facilitates significant advancements in reducing component weight. Techniques such as lattice structures and optimized designs ensure that parts remain strong while becoming lighter, enhancing fuel efficiency and performance. Moreover, the technology's ability to produce intricate internal structures and features, previously unattainable, vastly improves the functionality and effectiveness of components across a wide range of applications.
Types of Additive Manufacturing Technologies
Additive manufacturing encompasses a variety of innovative technologies, each tailored to specific materials and applications. These technologies provide unique solutions to manufacturing challenges, enhancing the capabilities of industries through their specialized processes.
Fused Deposition Modeling (FDM)
FDM is renowned for its simplicity and effectiveness in material extrusion. It operates by feeding a thermoplastic filament through a heated nozzle, which precisely lays down material layer by layer to form the object. This technology is widely used for crafting prototypes and practical parts due to its cost-effectiveness and the range of available materials like ABS and PLA. Its ease of use and adaptability make it a favored choice for small-scale production environments seeking to maximize efficiency without significant overhead.
Selective Laser Sintering (SLS) and Stereolithography (SLA)
SLS and SLA stand as pillars of advanced 3D printing techniques, each offering distinct advantages. SLS leverages a precise laser to fuse powdered materials, such as polyamide or metal composites, into solid structures, allowing for complex geometries with superior material properties. This method is particularly esteemed in industries demanding robust components. SLA, conversely, uses ultraviolet light to solidify liquid resin, producing parts with high precision and smooth finishes, ideal for applications where detail and aesthetics are paramount.
Direct Metal Laser Sintering (DMLS) / Selective Laser Melting (SLM) and Electron Beam Melting (EBM)
DMLS and SLM are instrumental in the production of high-quality metal parts. These processes employ lasers to meticulously melt and bond metal powders into dense components, ensuring strength and durability critical for sectors like aerospace and healthcare. Meanwhile, EBM utilizes an electron beam for similar purposes, offering advantages in energy efficiency and the capacity to create larger parts, making it suitable for aerospace applications where component size and integrity are crucial.
Binder Jetting
Binder Jetting offers a unique approach by employing a liquid binder to selectively adhere powder particles, forming complex parts layer by layer. This versatile technology accommodates a variety of materials, including metals and ceramics, enabling the production of intricate molds and detailed models. Its ability to fabricate components with varying densities and material compositions makes it a valuable asset in industries focused on precision and specificity, such as automotive manufacturing.
Materials Used in Additive Manufacturing
The breadth of additive manufacturing's capabilities is largely attributed to its use of a wide array of materials, each offering unique properties tailored to different industrial needs. This selection allows for the creation of specialized components that meet specific functional requirements.
Polymers and Advanced Thermoplastics
Polymers, particularly advanced thermoplastics, are fundamental in additive manufacturing. Materials such as PEEK and PEKK extend beyond traditional offerings like ABS and PLA, providing enhanced thermal and chemical resistance. These high-performance polymers are ideal for demanding environments, such as aerospace and medical applications, where material endurance under stress is critical. Their versatility supports the production of components requiring both precision and resilience.
High-Performance Metals
For applications necessitating exceptional strength and durability, high-performance metals like Inconel, titanium alloys, and maraging steel are frequently employed. These materials are crucial in sectors like defense and power generation, where they contribute to the development of parts that endure extreme conditions. The ability to produce complex metal components with superior mechanical properties enhances the operational capabilities of equipment in these industries.
Technical Ceramics and Composite Innovations
Technical ceramics such as silicon carbide and boron nitride are utilized for their high-temperature stability and wear resistance. These materials are essential in industries like electronics and energy, where they are used to fabricate components that must withstand harsh operating environments. On the other hand, composite innovations incorporating materials like graphene and nanotubes enhance the mechanical and electrical properties of conventional composites, offering new possibilities for lightweight and robust structural solutions.
Cutting-Edge Biomaterials
In the realm of healthcare, cutting-edge biomaterials are paving the way for advanced medical solutions. Materials like bioactive glass and collagen-based hydrogels are instrumental in tissue engineering and regenerative medicine. These biomaterials facilitate the development of scaffolds and implants that promote cell growth and integration, advancing the field of personalized medicine and improving patient outcomes through innovative, custom-fit medical devices.
Challenges and Limitations of Additive Manufacturing
Additive manufacturing faces several challenges that can impact its effectiveness and broader adoption across industries. One significant issue is the inherent limitations in production speed. Due to the layer-by-layer construction method, additive processes can be time-consuming compared to traditional manufacturing techniques that allow for quicker mass production. This slower pace can be a constraint, especially in scenarios where rapid turnaround is crucial.
The economic aspect of implementing additive manufacturing can also be a barrier. The upfront costs of acquiring advanced 3D printing equipment and the requisite materials can be considerable. This financial burden may deter smaller enterprises from fully embracing the technology, despite its potential for long-term gains. Additionally, ongoing operational expenses, including maintenance and material replenishment, add to the economic considerations that companies must navigate.
Physical constraints also pose challenges for additive manufacturing. The limited build volume of many 3D printers restricts the size of parts that can be produced in a single operation. This often necessitates assembling larger structures from multiple smaller components, which can introduce complexity and potential points of failure. Furthermore, issues such as anisotropic properties in the Z direction can affect the mechanical performance of parts, leading to potential weaknesses such as stress concentration or distortion during use.
The absence of comprehensive industry standards around additive manufacturing processes and materials further complicates its integration into various sectors. This lack of uniformity makes it challenging to ensure consistent quality and performance across different applications and industries. Establishing clear guidelines and standards is essential for fostering innovation and collaboration, as well as for building trust in the reliability of 3D-printed parts. Addressing these challenges requires concerted efforts from industry stakeholders, researchers, and regulatory bodies to develop robust frameworks that support the sustainable growth of additive manufacturing.
The Future of Additive Manufacturing
Additive manufacturing stands at the cusp of revolutionary changes, poised to deeply influence production landscapes. As the technology matures, its role in fabricating highly specialized end-use components becomes increasingly prominent. This evolution aligns with the introduction of next-generation 3D printers that offer substantial improvements in speed, scalability, and material versatility. These advanced machines not only cater to higher production demands but also maintain the agility needed for rapid design changes and customization.
Beyond hardware innovations, the development of comprehensive software solutions is reshaping the manufacturing workflow. Cutting-edge software platforms now offer enhanced capabilities in simulation, design optimization, and process automation. Such tools facilitate a more fluid transition from digital models to tangible products, minimizing errors and maximizing efficiency. This ongoing evolution in software is critical in supporting the integration of additive manufacturing into complex production ecosystems, ensuring seamless operations across diverse applications.
Material innovation continues to be a driving force behind the burgeoning potential of additive manufacturing. The advent of new material formulations, including high-strength polymers and bio-compatible composites, extends the applicability of 3D printing across various industries. This expansion is particularly significant in fields such as healthcare and aerospace, where material performance is paramount. As material science progresses, the potential for creating components with enhanced durability, functionality, and sustainability becomes increasingly attainable.
The adoption of hybrid manufacturing techniques, which blend additive and traditional methods, represents a strategic advancement in production efficiency. This approach leverages the strengths of both technologies, allowing for the creation of complex parts with superior surface finish and structural integrity. By integrating various manufacturing processes, companies can achieve higher productivity and more innovative product designs, paving the way for a future where manufacturing is both adaptable and precise.
As additive manufacturing continues to evolve, it's clear that this technology will play a crucial role in shaping the future of manufacturing. At Phasio, we're committed to helping businesses harness the full potential of additive manufacturing through our innovative software solutions and expert guidance. If you're ready to streamline your additive manufacturing workflows and unlock new possibilities, schedule a demo or try the platform to experience its capabilities firsthand.