Manufacturing with heart: Insights from Phasio's first Webinar with Eduard Siemens
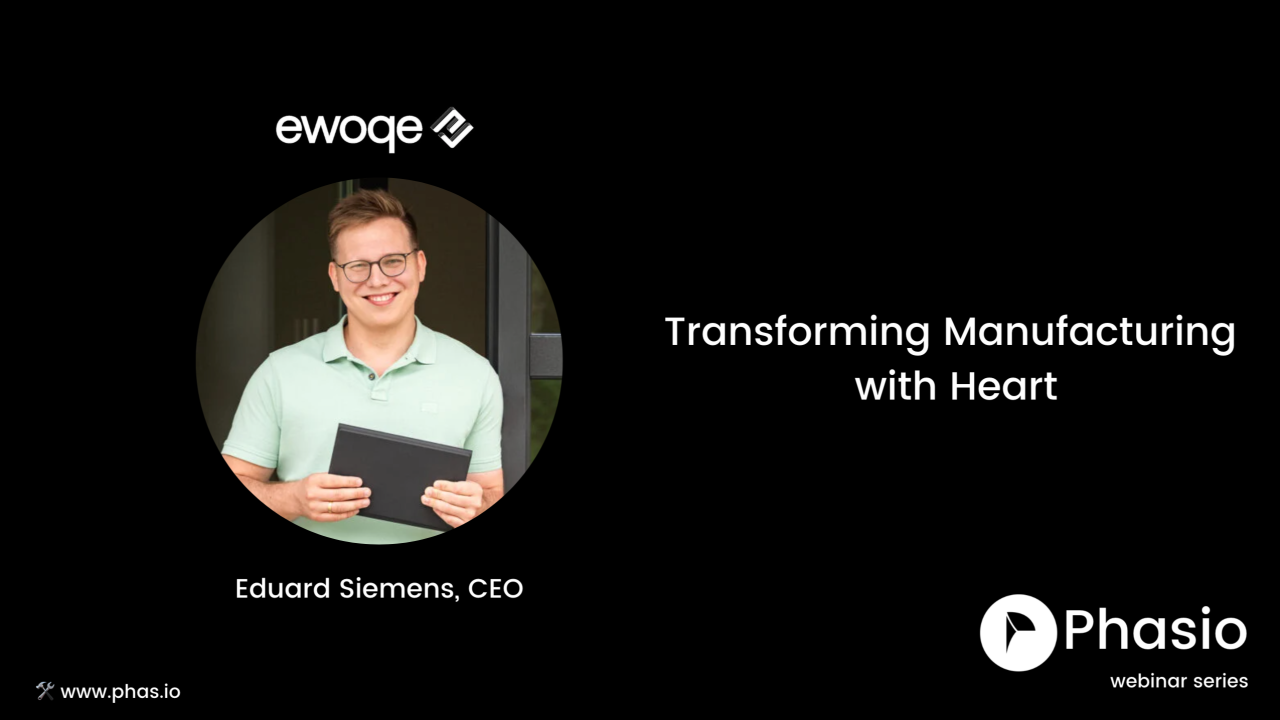
Manufacturing with heart: Insights from Phasio’s first Webinar with Eduard Siemens
Last month we had the honor of welcoming Eduard Siemens, CEO and founder of Ewoqe, to our very first Phasio webinar. Valuable insights from his vast experience across manufacturing setting up diverse production lines, offered a rare perspective into the soul of ethical manufacturing practices.
Culture-Driven Production: Eduard’s Philosophy
Eduard’s journey in the large-scale manufacturing sector highlights a critical lesson: the value of seeing people beyond numbers. He underscores the importance of making sure everyone in an organization understands the ‘why’ behind decisions, advocating for a culture-driven approach where every employee, from operators on the shop floor to senior management, is integral to the production quality. He highlights the importance of clear communication, transparency and accountability to maintain good quality production while keeping work conditions optimal.
Shifting Perspectives from Numbers to People
Eduard highlighted the stark reality of manufacturing’s human element. In his experiences — particularly with large contracts (e.g. he worked with IKEA at some point) — he saw how easy it was for workers to become mere figures on a spreadsheet. He recalled grueling 16+ hour shifts workers endured to meet the staggering demand for 10,000s of production items, a testament to the immense pressure exerted by major clients. All this while the very same clients demand open books, forcing timelines and squeezing the price point. Given that some of these would then occupy nearly 100% of production facilities’ capacity over multiple years, they essentially define and decide the fate of the workforce. This creates a power dynamic which could be framed as exploitative, and the lack of transparency made it so that people in Eduard’s position don’t even see the real impact of the numbers on the sheet until actually visiting those factories overseas.
This simultaneously marks a turning point in Eduard’s career. In visiting production facilities he’s managing he got to know firsthand how these data points on screen represent a person, with a family, dreams, and the need for respect and humane treatment. He saw the physical and emotional toll of the production-focused mindset optimising for profit, where the constant push for output led to burnout and a significant decrease in workplace morale, which then ultimately impacted quality.
Many production leaders and decision makers have a lack of empathy simply because of the disconnect across the different stakeholders. This epiphany led Eduard to advocate for a more humane approach, where employees are seen as valuable assets rather than disposable resources. He began to implement changes that focused not just on the output but on the wellbeing and satisfaction of each worker, understanding that this was the key to sustainable and ethical manufacturing. That then also led to the core principles behind founding his own company Ewoqe.
Small and Agile: The Blueprint for Future Manufacturing
Eduard’s vision for the future of manufacturing hinges on smaller, more agile units. He advocates for manufacturing setups of around 40–50 people, a size he believes is optimal for maintaining flexibility, responsiveness, and a tight-knit community. According to him, this approach allows for quicker adaptation to customer needs and market changes without overwhelming the workforce.
In these smaller units, Eduard sees a perfect balance between efficiency and quality. He notes that with fewer people each individual’s role becomes more significant, while their contribution more visible. Simultaneously this enables a closer relationship between the leadership team and the rest of the employees, as well as the manufacturer’s clients — leading to more effective communication and a deeper understanding of each person’s role in the bigger picture. Ultimately, Eduard points out that such setups allow for better work-life balance, reducing the risk of burnout and ensuring that employees remain motivated and committed. The type of positive energy that will ultimately also benefit the family and household of every person involved.
The Power of Communication and Context
For Eduard, effective communication is the backbone of successful manufacturing. He emphasized that clear, transparent communication based on radical candor across all levels of the hierarchy is essential to ensuring both quality and efficiency in production. This involves not only conveying decisions and directives from the top down but also encouraging feedback and input from the shop floor up, maintaining a healthy feedback loop.
Eduard illustrated this with examples from his own experience, where a lack of communication led to quality issues, missed deadlines, and a disconnected workforce. He speaks of a model where every team member, regardless of their position, is encouraged to speak openly and provide feedback — especially when things go wrong. This approach, he argued, not only helps in identifying and resolving issues quickly but also fosters a culture of mutual respect and collaboration.
Moreover, Eduard highlighted the importance of context in communication. He stressed that understanding the ‘why’ behind decisions and processes is as crucial as knowing the ‘what.’ This depth of understanding empowers employees, enabling them to see their work’s broader impact and fostering a sense of ownership and pride in their roles.
A New Era of Manufacturing
Eduard envisions a transformative model for the manufacturing industry, similar to the impact of Amazon in retail — a digital and operational revolution. He imagines a landscape where local manufacturers are not just surviving but thriving through enhanced control over their operations and deeper connections within their respective communities. This vision extends beyond mere technology adoption; it’s about reshaping the entire ecosystem of manufacturing and the networks formed therein.
Central to this vision is the concept of democratizing manufacturing technology. Eduard sees a future where even the smallest manufacturers have access to cutting-edge tools and resources, leveling the playing field with larger corporations. He speaks of a world where technology is not a barrier but an enabler — facilitating more efficient production methods, reducing waste, and increasing scalability without compromising the human touch.
In this new era, Eduard foresees a shift from mass production to customized, on-demand manufacturing. This approach not only meets the specific needs of customers but also fosters a more sustainable model of production. By leveraging technologies like 3D printing and advanced automation, manufacturers can reduce inventory costs, minimize waste, and respond swiftly to market changes.
Transforming Challenges into Opportunities
In the webinar, Eduard shared real-life scenarios where challenges were converted into opportunities for growth and improvement. A key aspect of this transformation is creating a work culture that values and supports employee wellbeing. Eduard highlighted how treating employees as key stakeholders rather than mere cogs in the machine leads to a more engaged, motivated, and productive workforce.
Eduard’s approach to challenge transformation is deeply analytical yet human-centric. He delves into the roots of problems, be it in communication breakdowns, process inefficiencies, or technology gaps. By doing so, he identifies areas where small but strategic changes can lead to significant improvements.
Phasio’s Role in This Transformative Journey
At Phasio, we align closely with Eduard’s vision. Our tools and software, designed to enhance the efficiency and communication in manufacturing processes, play a pivotal role in this transformation. We aim to provide solutions that support Eduard’s vision of ethical, efficient, and human-centric manufacturing, ensuring that technological advancements work hand in hand with the well-being of those in the manufacturing sector.
One example he gave is that by bringing in Phasio’s software, he is now saving 5 hours daily in writing quotations. That frees up more time to bring in more business, spend more time on strategically building out his business, care for his employee wellbeing, etc.
An Invitation to Join the Ethical Manufacturing Movement
As we continue our series of webinars, we invite you to join us in this journey towards a more ethical and connected manufacturing future — both in the technological and human realm. If Eduard’s story has inspired you, and you’re curious about how these principles can be applied to your business, reach out to us. Together, let’s build a future where manufacturing is not just about products, but people and purpose.
🛠️ Happy manufacturing!
PS: if you have any wishes for a potential webinar, someone you'd like to see or topic discussed, don't hesitate to drop us a line at hello@phas.io